Contact Details
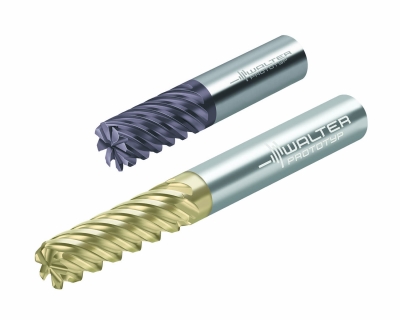
Walter has introduced two new multi-tooth solid carbide face milling cutters, the MC128 Advance and the MD128 Supreme, for finishing and semi-finishing, with a secondary use for dynamic milling. These close-pitch cutters produce excellent surfaces, with minimal burr formation on the component primarily thanks to a 50° helix. Both excel at the finishing of shoulders, pockets, walls, and cavities. They feature protective chamfer or a corner radii with cylindrical shank. A ConeFit exchangeable head is also available with each.
The MC128 Advance boasts a wide diameter range of 1/4 -3/4 in. (2-25 mm) with a TiAIN coating for universal use. WJ30TF grade is available for ISO materials P, M, K, and S. The MC128 Advance is well suited for die and mold work as well as general metalworking. The MD128 Supreme provides 64% more tool life when compared to similar competitive cutters. It is a close pitch cutter providing maximum productivity thanks to more teeth, a longer cutting-edge length and material-specific grades. It is intended for semi-finishing and finishing, including finishing of additively manufactured components and of dynamically roughed components up to 3 × Dc (ConeFit 1.5 x Dc). Its material-specific grades are: WJ30RD (AITiN + ZrN) for ISO P material and WJ30RA (TiAIN + TiAI)for ISO materials M and S. This allows the grade to be adapted to the specific material group. Diameter range is 6-25 mm. With use in deep cavities, thanks to ConeFit tools, it can be successfully employed in medical technology, the aerospace, and energy industries, and die and mold.
The Walter lineup of products consists of three categories to its tools. Supreme indicates the highest level of technology and performance available. Perform tools are products that provide an economical solution with focused importance on price and Advance which indicates product efficiently balanced between price and performance.
Related Glossary Terms
- burr
burr
Stringy portions of material formed on workpiece edges during machining. Often sharp. Can be removed with hand files, abrasive wheels or belts, wire wheels, abrasive-fiber brushes, waterjet equipment or other methods.
- gang cutting ( milling)
gang cutting ( milling)
Machining with several cutters mounted on a single arbor, generally for simultaneous cutting.
- metalworking
metalworking
Any manufacturing process in which metal is processed or machined such that the workpiece is given a new shape. Broadly defined, the term includes processes such as design and layout, heat-treating, material handling and inspection.
- milling
milling
Machining operation in which metal or other material is removed by applying power to a rotating cutter. In vertical milling, the cutting tool is mounted vertically on the spindle. In horizontal milling, the cutting tool is mounted horizontally, either directly on the spindle or on an arbor. Horizontal milling is further broken down into conventional milling, where the cutter rotates opposite the direction of feed, or “up” into the workpiece; and climb milling, where the cutter rotates in the direction of feed, or “down” into the workpiece. Milling operations include plane or surface milling, endmilling, facemilling, angle milling, form milling and profiling.
- pitch
pitch
1. On a saw blade, the number of teeth per inch. 2. In threading, the number of threads per inch.
- shank
shank
Main body of a tool; the portion of a drill or similar end-held tool that fits into a collet, chuck or similar mounting device.