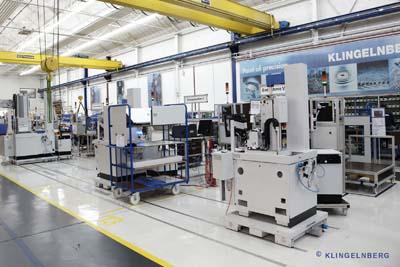
Klingelnberg was prominent in bringing high-precision measurement machines from the test room onto the shop floor, thus essentially propelling the realization of efficiency concepts in manufacturing lines. Now, the company has implemented an own assembly line for five series of precision measuring centers in Hueckeswagen, Germany. The logistics concept was developed and implemented by STROTHMANN.
Via RoundTracks, the machines, which are based on a modular system and configured according to the customers' measuring tasks, are moved from station to station in one-piece-flow. The cycle time is one day. Previously, the sensitivity of the measuring instruments would only permit box assembly. STROTHMANN solved this particular challenge with special carts which are lowered onto leveling platforms at the workstations. A short supply of compressed air lifts the carts onto driving level again, a locking lever holds that position.
Final assembly, which used to have no fixed time span, now takes ten days at maximum. Machines that are part of one commission are scheduled for delivery directly after they are completed. Thus, throughput time and capital commitment were decreased at once. STROTHMANN supports customers in the implementation of efficiency concepts from the early planning stages all the way through to the commissioning of complex assembly lines. The handling expert can draw on mechanical engineering expertise and an extensive project portfolio including turnkey solutions for all kinds of industry sectors. Users of the patented RoundTrack technology appreciate the precise running and wear-resistance of the intra-logistics transport medium.
Markus Friedrich, assembly manager at Klingelnberg, says: "The best thing is the simplicity of this logistics technology. It does the job, is extremely smooth-running and resilient at the same time. Taken together, this ensures high reliability and availability."
The follow-up project is also well on track: currently, Klingelnberg is implementing with STROTHMANN a manufacturing line for four types of gear cutting machines in its headquarters in Switzerland.
Contact Details
Related Glossary Terms
- centers
centers
Cone-shaped pins that support a workpiece by one or two ends during machining. The centers fit into holes drilled in the workpiece ends. Centers that turn with the workpiece are called “live” centers; those that do not are called “dead” centers.