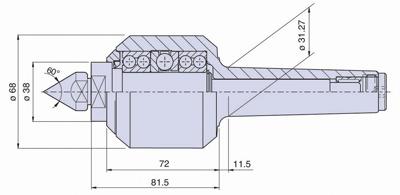
To help machine shops reduce their production costs and improve efficiency, ITA offers high-quality PTM Live Centers and Dead Centers that come with a wide selection of interchangeable points for a variety of applications.
"While interchangeable points are not a new concept, at ITA we stock a greater selection of sizes and shapes than many of our competitors," says a company spokesperson. "Our customers like this because they can use the same center for a number of workholding applications, simply changing the point for a new application, or replacing it when it wears out instead of replacing the whole center. The cost savings are significant."
ITA carries the PTM line of Live Centers and Dead Centers not only for their diverse assortment of interchangeable points, but because they manufacture centers that deliver highly-accurate, long-lasting performance at a low price. This allows users of PTM centers to reduce their workpiece holding and retooling costs, while increasing the accuracy of their turning, grinding, gear-cutting and other metalworking operations.
Each PTM Live Center and Dead Center is engineered for maximum tool clearance while providing the highest rigidity to the workpiece. And where required, permanent lubricating grease and specially designed seals are used, guaranteed to keep out machining fines and coolants, even high-pressure coolant. Through the use of quality materials, innovative design and efficient manufacturing processes, PTM is able to produce superior components at significant savings, which ITA then passes along to its customers.
ITA also offers custom centers to meet a customer's specific requirements, with quick turnaround at reasonable prices. "We pride ourselves on our customer service," the spokesperson adds. "Our knowledgeable experts are happy to answer any questions about the particular machining needs our customers may have. Very often, we're able to recommend products and accessories that perform a lot better and offer greater savings than the ones they had in mind."
Contact Details
Related Glossary Terms
- centers
centers
Cone-shaped pins that support a workpiece by one or two ends during machining. The centers fit into holes drilled in the workpiece ends. Centers that turn with the workpiece are called “live” centers; those that do not are called “dead” centers.
- clearance
clearance
Space provided behind a tool’s land or relief to prevent rubbing and subsequent premature deterioration of the tool. See land; relief.
- coolant
coolant
Fluid that reduces temperature buildup at the tool/workpiece interface during machining. Normally takes the form of a liquid such as soluble or chemical mixtures (semisynthetic, synthetic) but can be pressurized air or other gas. Because of water’s ability to absorb great quantities of heat, it is widely used as a coolant and vehicle for various cutting compounds, with the water-to-compound ratio varying with the machining task. See cutting fluid; semisynthetic cutting fluid; soluble-oil cutting fluid; synthetic cutting fluid.
- grinding
grinding
Machining operation in which material is removed from the workpiece by a powered abrasive wheel, stone, belt, paste, sheet, compound, slurry, etc. Takes various forms: surface grinding (creates flat and/or squared surfaces); cylindrical grinding (for external cylindrical and tapered shapes, fillets, undercuts, etc.); centerless grinding; chamfering; thread and form grinding; tool and cutter grinding; offhand grinding; lapping and polishing (grinding with extremely fine grits to create ultrasmooth surfaces); honing; and disc grinding.
- metalworking
metalworking
Any manufacturing process in which metal is processed or machined such that the workpiece is given a new shape. Broadly defined, the term includes processes such as design and layout, heat-treating, material handling and inspection.
- turning
turning
Workpiece is held in a chuck, mounted on a face plate or secured between centers and rotated while a cutting tool, normally a single-point tool, is fed into it along its periphery or across its end or face. Takes the form of straight turning (cutting along the periphery of the workpiece); taper turning (creating a taper); step turning (turning different-size diameters on the same work); chamfering (beveling an edge or shoulder); facing (cutting on an end); turning threads (usually external but can be internal); roughing (high-volume metal removal); and finishing (final light cuts). Performed on lathes, turning centers, chucking machines, automatic screw machines and similar machines.