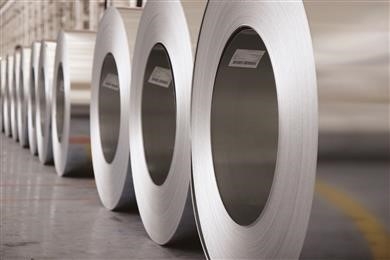
With more than 80 years of expertise in the metal processing/coil industry and an extensive range of process solutions for pickling, lubrication, cleaning, pretreatment, passivation, coating and lamination, Henkel has firmly established itself as a global one-stop partner of the metal coil industry. New product innovations are strongly focused on helping customers manage the process needs of next-generation alloys while meeting cost and regulatory challenges.
Metal is used in a range of diversified end markets from automotive and transportation, building and construction, appliances and general industry to power and electrical as well as food and beverage. In addition, growing urbanization is creating demands for everyday applications in various emerging market segments. Henkel’s comprehensive process solutions for this demanding industry are specially formulated for high-speed and continuous operation of manufacturing lines. At the same time, they address ambitious drives for greater cost-efficiency and sustainability.
“There is a clear trend in the metal coil industry towards greater process and cost control. And while new high-strength steel, aluminum and magnesium alloys open opportunities for increased lightweighting, sheet metal manufacturers and coaters are faced with ever stricter environmental regulations ” says Aziz Mabrouki, business director Metal Coil Europe for Henkel. “Based on our close collaboration with industry leaders, we offer customers a one-stop portfolio of process solutions meeting these challenges. Overall benefits include cost savings through longer bath and tool lives, elimination of chromium, nitrate in waste water and NOx emissions as well as reduced waste. Moreover, Henkel also provides special equipment designed to ensure best manufacturing practices in many coil process steps.”
Henkel’s Bonderite portfolio of efficient, safe and sustainable solutions for the metal coil manufacturing chain includes:
- Pickling inhibitors, added to hydrochloric or sulfuric acid to avoid over-pickling and provide a uniform surface for the next process step
- Cold rolling oils, for best lubrication results resulting in high productivity and high sheet quality
- Cleaners, designed to remove grease, oil and metal fines from the sheet surface to prepare it for the next step
- Wet temper fluids, used to increase the life time of work rolls and provide adequate corrosion protection for intermediate storage
- Surface treatment agents, preparing the substrate for reliable paint adhesion and adding excellent corrosion protection
- Passivates, applied to galvanized sheet and tin plate products to avoid corrosion during storage and transport
- Thin organic coatings, providing anti-fingerprint and other effective properties for decorative surfaces as well as improved weldability and forming
Additionally, Henkel offers adhesives, engineered for reliable and cost-effective coil lamination in compliance with latest environmental regulations.
In all of these product lines, the company’s innovation focus is on developing and providing value-added solutions targeted at delivering higher productivity as well as extending the lifetime of work rolls during rolling and skin passing as well as in four key areas: Chromium-free formulations for a broad range of more sustainable paint technologies; cost-effective products such as adhesion promoters, Cr-free organic coatings, forming and stamping aids for new alloys and substrates; nitric acid free pickling and solutions for low-fluoride pickling processes to reduce overall operating and waste water treatment costs. A full range of pretreatment agents and adhesives for process and downstream cost savings in an increasingly diversified coil lamination market is also available.
“The use of chromium (VI) has already been restricted in Europe, with further prohibitions to come. We are committed to helping our customers enhance the sustainability of their production by moving to highly effective solutions free of heavy metals and in high concentrations designed to reduce consumption and waste while optimizing their processes,” adds Mabrouki. “Henkel has a history of 20 years in chromium-free products for painted sheet, and has successfully extended the technology to other processes, such as passivation.”
Contact Details
Related Glossary Terms
- alloys
alloys
Substances having metallic properties and being composed of two or more chemical elements of which at least one is a metal.
- titanium nitride ( TiN)
titanium nitride ( TiN)
Added to titanium-carbide tooling to permit machining of hard metals at high speeds. Also used as a tool coating. See coated tools.