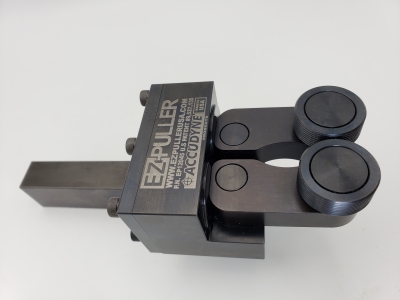
Accudyne Products introduces its Expanded Capacity bar puller for CNC lathe automation. The new EZ-Puller Expanded Capacity supports larger round bar diameters of .093” to 2.00" and weighs of up to 100lbs. Hex bar capacity of .250" to 1.375", and square bar capacity of .250" to 1.000" are pulled without an M19 (spindle orientation) function.
The EZ-Puller is an auto-adjusting bar puller that enables automatic operation of CNC lathes. The auto adjust feature is driven by an "X" value in the pulling subroutine of a lathe program. This value represents the distance the tool needs to move in the X-axis according to the bar diameter being pulled.
The patented design of the EZ-Puller uses a cam and lifter system. Hardened steel grippers are attached to hardened steel pivot arms. These arms have an integral cam lobe machined at the top of the arm. As the grippers advance over the bar stock, internal urethane springs are compressed. The urethane springs provide a reactive force that allows the grippers to securely hold the bar stock. This unique design provides optimal gripping force regardless of bar size or shape.
Other features of the EZ-Puller are that it will accommodate an infinite range of sizes within its capacity without mechanical adjustment, allowing for multiple pulls. Multiple pulls are used for longer parts that cannot be cost-effectively machined in one chucking. The design of the EZ-Puller also allows for pulling bars with minimal projection in front of the work-holding chuck. This characteristic allows the machinist to set-up with as little as two gripper serrations (.120”) of engagement which makes for a more rigid setup.
Related Glossary Terms
- chuck
chuck
Workholding device that affixes to a mill, lathe or drill-press spindle. It holds a tool or workpiece by one end, allowing it to be rotated. May also be fitted to the machine table to hold a workpiece. Two or more adjustable jaws actually hold the tool or part. May be actuated manually, pneumatically, hydraulically or electrically. See collet.
- computer numerical control ( CNC)
computer numerical control ( CNC)
Microprocessor-based controller dedicated to a machine tool that permits the creation or modification of parts. Programmed numerical control activates the machine’s servos and spindle drives and controls the various machining operations. See DNC, direct numerical control; NC, numerical control.
- computer-aided manufacturing ( CAM)
computer-aided manufacturing ( CAM)
Use of computers to control machining and manufacturing processes.
- lathe
lathe
Turning machine capable of sawing, milling, grinding, gear-cutting, drilling, reaming, boring, threading, facing, chamfering, grooving, knurling, spinning, parting, necking, taper-cutting, and cam- and eccentric-cutting, as well as step- and straight-turning. Comes in a variety of forms, ranging from manual to semiautomatic to fully automatic, with major types being engine lathes, turning and contouring lathes, turret lathes and numerical-control lathes. The engine lathe consists of a headstock and spindle, tailstock, bed, carriage (complete with apron) and cross slides. Features include gear- (speed) and feed-selector levers, toolpost, compound rest, lead screw and reversing lead screw, threading dial and rapid-traverse lever. Special lathe types include through-the-spindle, camshaft and crankshaft, brake drum and rotor, spinning and gun-barrel machines. Toolroom and bench lathes are used for precision work; the former for tool-and-die work and similar tasks, the latter for small workpieces (instruments, watches), normally without a power feed. Models are typically designated according to their “swing,” or the largest-diameter workpiece that can be rotated; bed length, or the distance between centers; and horsepower generated. See turning machine.