Contact Details
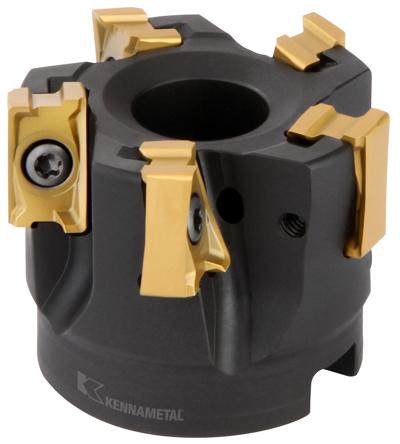
Experienced manufacturers know that when milling, three main considerations predominate: metal removal rate, tool life, and surface finish. All three are critical to successful metalworking, but often one will predominate. Manufacturers facing parts requiring 90-degree shoulders also know that achieving true 90-degree shoulders and minimizing the scallop or step marks between passes absolutely requires a high-performance cutter.
The new Mill 4-15 platform from Kennametal is that best-in-class system, according to the company. Mill 4-15 features a double-sided insert with four cutting edges for effective cost per edge and able to take up to 15mm [.590"] depth of cut, while a unique cutting edge design assures positive contact through 90-degree milling and virtually "stepless" solution for stepping-down applications. In addition, an integrated wiper facet achieves best-in-class surface finishes.
"After its development, it's safe to say Mill 4-15 is a definite game-changer," says Juan Seculi, Kennametal indexable milling product manager. "Between the cutter body and insert features available, customers can be assured of high value from the best product available"
Mill 4-15 inserts will be available precision ground or molded inserts with corner nose radii from 0.4mm to 2.4mm. Topographies include GE with a high positive rake, effectively lowering cutting forces while reinforced cutting edge emphasizes cutting-edge strength for medium to heavy applications. Mill 4-15 cutter bodies are manufactured to very tight tolerances. Multiple cutter body options, including screw-on, cylindrical shank end mills, Weldon shank end mills, and shell mill cutters with effective internal coolant feature are available.
"Companies are often forced to trade off work efficiency, surface quality, or overall cost in shoulder milling," Seculi says. "Mill 4-15 offers a universal solution for a majority of workpiece materials in a cost-effective, multiedge design. Now there are no compromises."
Related Glossary Terms
- coolant
coolant
Fluid that reduces temperature buildup at the tool/workpiece interface during machining. Normally takes the form of a liquid such as soluble or chemical mixtures (semisynthetic, synthetic) but can be pressurized air or other gas. Because of water’s ability to absorb great quantities of heat, it is widely used as a coolant and vehicle for various cutting compounds, with the water-to-compound ratio varying with the machining task. See cutting fluid; semisynthetic cutting fluid; soluble-oil cutting fluid; synthetic cutting fluid.
- depth of cut
depth of cut
Distance between the bottom of the cut and the uncut surface of the workpiece, measured in a direction at right angles to the machined surface of the workpiece.
- gang cutting ( milling)
gang cutting ( milling)
Machining with several cutters mounted on a single arbor, generally for simultaneous cutting.
- metalworking
metalworking
Any manufacturing process in which metal is processed or machined such that the workpiece is given a new shape. Broadly defined, the term includes processes such as design and layout, heat-treating, material handling and inspection.
- milling
milling
Machining operation in which metal or other material is removed by applying power to a rotating cutter. In vertical milling, the cutting tool is mounted vertically on the spindle. In horizontal milling, the cutting tool is mounted horizontally, either directly on the spindle or on an arbor. Horizontal milling is further broken down into conventional milling, where the cutter rotates opposite the direction of feed, or “up” into the workpiece; and climb milling, where the cutter rotates in the direction of feed, or “down” into the workpiece. Milling operations include plane or surface milling, endmilling, facemilling, angle milling, form milling and profiling.
- milling machine ( mill)
milling machine ( mill)
Runs endmills and arbor-mounted milling cutters. Features include a head with a spindle that drives the cutters; a column, knee and table that provide motion in the three Cartesian axes; and a base that supports the components and houses the cutting-fluid pump and reservoir. The work is mounted on the table and fed into the rotating cutter or endmill to accomplish the milling steps; vertical milling machines also feed endmills into the work by means of a spindle-mounted quill. Models range from small manual machines to big bed-type and duplex mills. All take one of three basic forms: vertical, horizontal or convertible horizontal/vertical. Vertical machines may be knee-type (the table is mounted on a knee that can be elevated) or bed-type (the table is securely supported and only moves horizontally). In general, horizontal machines are bigger and more powerful, while vertical machines are lighter but more versatile and easier to set up and operate.
- rake
rake
Angle of inclination between the face of the cutting tool and the workpiece. If the face of the tool lies in a plane through the axis of the workpiece, the tool is said to have a neutral, or zero, rake. If the inclination of the tool face makes the cutting edge more acute than when the rake angle is zero, the rake is positive. If the inclination of the tool face makes the cutting edge less acute or more blunt than when the rake angle is zero, the rake is negative.
- shank
shank
Main body of a tool; the portion of a drill or similar end-held tool that fits into a collet, chuck or similar mounting device.
- wiper
wiper
Metal-removing edge on the face of a cutter that travels in a plane perpendicular to the axis. It is the edge that sweeps the machined surface. The flat should be as wide as the feed per revolution of the cutter. This allows any given insert to wipe the entire workpiece surface and impart a fine surface finish at a high feed rate.