Contact Details
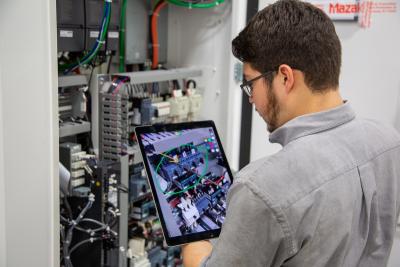
With the launch of its new MPower customer support program, Mazak takes complete customer care to the next level, giving manufacturers the tools they need to achieve their business goals and ensure continued success. With MPower, Mazak customers gain fast and accurate replacement parts ordering and service scheduling along with direct, real-time access to Mazak for a multitude of support benefits. Those include expert technical service through the company’s Remote Assist Services and on-demand training with its Learning Management System in addition to local support from a network of Technology and Technical Centers and Mazak’s cost-effective Spindle Rebuilding Services.
Through Mazak’s eight Technology Centers and five Technical Centers located throughout North America, the MPower program also gives customers convenient and local access to additional support. The centers are a place for advanced applications support, education and training, new technology demonstrations and special manufacturing events.
According to Mazak President Dan Janka, MPower is Mazak’s single-source, end-to-end customer support that it provides for the life of every machine. “The program helps shops save even more time and money in terms of service and support,” he said, “and it demonstrates our true commitment to customers and shows that Mazak is with them every step of the way, fully invested in their success.”
To streamline replacement parts ordering, MPower enables shops to digitally connect with Mazak and view an online image of the part along with its price, then easily place an order from Mazak’s inventory of more than 500,000 unique part numbers in stock and receive next day delivery. In the near future, shops will be able to simply pull up their specific machine model and serial number, and Mazak will cross reference the part number to ensure the correct replacement. This information can be obtained currently with one phone call.
For machine service, shops can now log on to the new My Mazak service portal in real time to access account information, open a work order, check the availability of the next service technician or resolve the issue over the phone with tech support. When an in-person service call is scheduled, shops can check on the status of an existing work order or track when to expect the service technician to arrive.
Time is money for today’s manufacturers, and Mazak’s Remote Assist service shortens the mean time to repair and reduces the costs associated with in-person field service calls. Once a customer downloads a simple mobile or web app, a technician (located at one of Mazak’s Technology Centers, Technical Centers or at its Florence, Kentucky-based headquarters) can then interact with the shop’s connected devices to send specific work instructions and communicate with the shop just as in a face-to-face service call.
When a machine repair requires parts, shops can also use Remote Assist to identify the correct replacement so Mazak can ship it to a field service technician for direct installation. This process eliminates an in-person diagnostics visit before the parts order, saving an average of two days of downtime. In addition to combining diagnostics and part orders into a single virtual visit, Mazak's Remote Assist offers three-way connections that let service technicians collaborate on solutions with other experts.
Because spindles are the heart of every machine tool, Mazak’s Spindle Rebuild Department offers customers fast and precise spindle rebuilding services under the MPower umbrella. The department has the ability to refurbish over 700 machine spindle variations drawing from a more than $54 million dedicated spindle inventory. Once rebuilt, spindles are warrantied for one year or 4,000 hours.
Mazak’s on-demand Learning Management System allows users to custom-tailor training programs, select subject matter from over 100 multi-level courses and schedule classes for times that suit their schedules, especially when in-person instruction becomes impossible or inconvenient. Through MPower, the system makes essential courses accessible on demand to shops anytime, anywhere.
The Learning Management System offers online instruction and virtual experiences that provide all the engagement of in-person instruction with the same standards of results. It also enables Mazak to customize its course offerings and subject matter to meet customer requests and adapt classes to suit learning levels. This ensures that shops always have access to exactly the right classes that will empower their teams to do more.
Related Glossary Terms
- centers
centers
Cone-shaped pins that support a workpiece by one or two ends during machining. The centers fit into holes drilled in the workpiece ends. Centers that turn with the workpiece are called “live” centers; those that do not are called “dead” centers.
- web
web
On a rotating tool, the portion of the tool body that joins the lands. Web is thicker at the shank end, relative to the point end, providing maximum torsional strength.