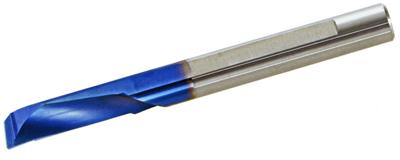
The latest addition to the Carmex Tiny Tool line—the multi-task CMR—allows users to bore, turn, face and chamfer with a single tool. The unique cutting geometry reportedly permits machining without the need for a pilot hole, thereby saving the time and expense of an entire operation. Designed with a vertical coolant hole and a spiral flute, the CMR continually evacuates chips out of the hole during machining.
"The new CMR Tiny Tool not only shortens machine cycle time but, thanks to the variety of operations it performs, it saves money on tooling," according to Jeff Dei, president of Carmex USA. "Submicron carbide, coupled with BMK grade carbide and advanced PVD triple layer coating, improves finish and yields longer life. CMR delivers unprecedented versatility, combined with productivity and dollar savings."
Contact Details
Related Glossary Terms
- coolant
coolant
Fluid that reduces temperature buildup at the tool/workpiece interface during machining. Normally takes the form of a liquid such as soluble or chemical mixtures (semisynthetic, synthetic) but can be pressurized air or other gas. Because of water’s ability to absorb great quantities of heat, it is widely used as a coolant and vehicle for various cutting compounds, with the water-to-compound ratio varying with the machining task. See cutting fluid; semisynthetic cutting fluid; soluble-oil cutting fluid; synthetic cutting fluid.
- physical vapor deposition ( PVD)
physical vapor deposition ( PVD)
Tool-coating process performed at low temperature (500° C), compared to chemical vapor deposition (1,000° C). Employs electric field to generate necessary heat for depositing coating on a tool’s surface. See CVD, chemical vapor deposition.