Contact Details
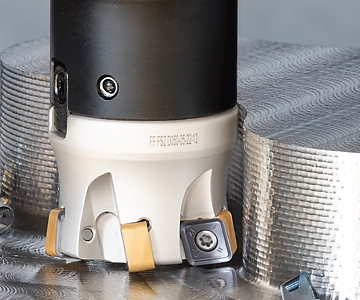
The new NEOFEED cutters are available in the diameter range 2.00”-4.00” in the following two shell-mill design configurations:
- FFQ8 -12 with 12° cutting edge angle for extremely high feed per tooth (fast feed milling) at depths of cut up of to .059”.
- MFQ8 -12 with 22° cutting edge angle for milling with “moderate” feed milling (less than high but much more than common) at depths of cut up of to .118”.
- When milling near a wall using MFQ8 D...-12 cutter up-milling is recommended.
The new shell mills carry the same double-sided square inserts FFQ8 SZMU 120520… with 8 cutting edges.
When mounted in a NEOFEED tool, the insert enables a positive tool rake angle which assures smooth cutting and reduced cutting forces and power consumption. The insert pocket has a dovetail shape that provides rigid and reliable insert clamping and improves the a cutter’s capability to withstand heavy load. These features provide increased cutting data for better productivity and for improved tool life.
The new FFQ8/MFQ8 D…-12 shell mill cutters feature a fine-pitch option for 2.00 - 4.00” cutters. This feature extends the range of application options for roughing specifically in the Die & Mold, Aerospace and general engineering industries.
FFQ8 SZMU 120520… Insert Features
- Double-sided square insert with 8 cutting edges.
- High-strength body structure.
- The specially designed .0787” radius insert corner with reinforced cutting edge increases insert strength when milling near a wall.
- Available with two types of cutting geometries (T/HP) for optimal machining different materials.
- FFQ8 SZMU 120520... inserts are produced from ISCAR’s latest carbide grades with post-coating treatment technologies that guarantee greater tool life and higher productivity.
- The same insert fits the both types of the new cutters.
- An attractive economical solution due to insert cost effectiveness per one cutting edge.
FFQ8 SZMU 120520T - for steel, ferritic and martensitic stainless steel, cast iron and hardened steel (ISO P, K and H groups of application).
FFQ8 SZMU 120520HP - for austenitic stainless steel and high temperature alloys (ISO M and S groups of application).
FFQ8/MFQ8 D…-12 Cutter Features
- FFQ8/MFQ8 D…-12 A fine-pitch design for increased metal removal rates.
- Coolant holes directed to each cutting edge, for efficient coolant and improved productivity.
- Protective coating of a cutter’s body provides better chip flow and protection from corrosion and wear.
Cutting data
The recommended cutting data are shown in the tables in the last pages.
NEOFEED
An advantageous tool for productive and cost-efficient rough milling
FFQ8-12
Fast Feed Face Mills Carrying Double-Sided Inserts with 8 Cutting Edges
• Radius for programming .142"
• To generate a straight surface without cusps, the width of cut most not exceed DC
• For slot milling or machining with high tool overhang, the maximum depth of cut should be reduced by 30%
(1) Cutting diameter maximum
(2) Number of inserts
(3) Maximum ramping angle
(4) For interpolation
(5) For interpolation
(6) Master insert identification
MFQ8-12
Moderate Feed Face Mills Carrying Double-Sided Inserts with 8 Cutting Edges
• Radius for programming .197"
• To generate a straight surface without cusps, the width of cut most not exceed DC
• For slot milling or machining with high tool overhang, the maximum depth of cut should be reduced by 30%.
(1) Cutting diameter maximum
(2) Number of inserts
(3) Master insert identification
FFQ8 SZMU
Square Double-Sided Inserts with 8 Cutting Edges for High Feed Milling
• For side plunging, the initial cutting feed is 0.1 mm/t
• T- for steel, ferritic and martensitic stainless steel, cast iron and hardened steel
• HP - for austenitic stainless steel and high temperature alloys.
Averaged cutting data for FFQ8 fast feed cutters
* ISCAR material group in accordance with VDI 3323 standard
** Quenched and tempered
For machining in unstable conditions, the recommended cutting data should be reduced by 20-30%.
Related Glossary Terms
- alloys
alloys
Substances having metallic properties and being composed of two or more chemical elements of which at least one is a metal.
- coolant
coolant
Fluid that reduces temperature buildup at the tool/workpiece interface during machining. Normally takes the form of a liquid such as soluble or chemical mixtures (semisynthetic, synthetic) but can be pressurized air or other gas. Because of water’s ability to absorb great quantities of heat, it is widely used as a coolant and vehicle for various cutting compounds, with the water-to-compound ratio varying with the machining task. See cutting fluid; semisynthetic cutting fluid; soluble-oil cutting fluid; synthetic cutting fluid.
- depth of cut
depth of cut
Distance between the bottom of the cut and the uncut surface of the workpiece, measured in a direction at right angles to the machined surface of the workpiece.
- feed
feed
Rate of change of position of the tool as a whole, relative to the workpiece while cutting.
- gang cutting ( milling)
gang cutting ( milling)
Machining with several cutters mounted on a single arbor, generally for simultaneous cutting.
- interpolation
interpolation
Process of generating a sufficient number of positioning commands for the servomotors driving the machine tool so the path of the tool closely approximates the ideal path. See CNC, computer numerical control; NC, numerical control.
- milling
milling
Machining operation in which metal or other material is removed by applying power to a rotating cutter. In vertical milling, the cutting tool is mounted vertically on the spindle. In horizontal milling, the cutting tool is mounted horizontally, either directly on the spindle or on an arbor. Horizontal milling is further broken down into conventional milling, where the cutter rotates opposite the direction of feed, or “up” into the workpiece; and climb milling, where the cutter rotates in the direction of feed, or “down” into the workpiece. Milling operations include plane or surface milling, endmilling, facemilling, angle milling, form milling and profiling.
- milling machine ( mill)
milling machine ( mill)
Runs endmills and arbor-mounted milling cutters. Features include a head with a spindle that drives the cutters; a column, knee and table that provide motion in the three Cartesian axes; and a base that supports the components and houses the cutting-fluid pump and reservoir. The work is mounted on the table and fed into the rotating cutter or endmill to accomplish the milling steps; vertical milling machines also feed endmills into the work by means of a spindle-mounted quill. Models range from small manual machines to big bed-type and duplex mills. All take one of three basic forms: vertical, horizontal or convertible horizontal/vertical. Vertical machines may be knee-type (the table is mounted on a knee that can be elevated) or bed-type (the table is securely supported and only moves horizontally). In general, horizontal machines are bigger and more powerful, while vertical machines are lighter but more versatile and easier to set up and operate.
- rake
rake
Angle of inclination between the face of the cutting tool and the workpiece. If the face of the tool lies in a plane through the axis of the workpiece, the tool is said to have a neutral, or zero, rake. If the inclination of the tool face makes the cutting edge more acute than when the rake angle is zero, the rake is positive. If the inclination of the tool face makes the cutting edge less acute or more blunt than when the rake angle is zero, the rake is negative.
- width of cut
width of cut
Width of the milled surface, reflecting a face milling cutter’s radial engagement, and a peripheral milling cutter’s axial engagement, in the cut.