Contact Details
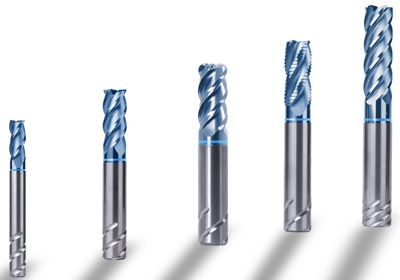
The HAIMER-developed endmill geometries are based on an unequal flute and helix design for chatter-free high-end machining, according to the company. All tools are coated with latest PVD technology and have an extremely smooth surface for enhanced chip evacuation.
The new HAIMER Power Mill range, with cutting diameters available from 2mm to 20mm, will be made available with 3, 4 and 5 cutting edges having multiple lengths of cut. To offer maximum flexibility in order to address the customers application requirements, different cutting edge solutions (sharp, chamfer and radius) will be offered. Also a roughing geometry with a cord profile will be part of the portfolio.
A typical HAIMER specialty is the high precision of the tools. All end mills are fine balanced and have a run-out of 5µm. All shanks are based on the h5 tolerance.
With the launch of the new Power Mill range HAIMER has expanded the Safe-Lock offering. Resulting from the wide spread and multiple customer requests for different application areas, Safe-Lock will be available starting from shank diameter 6mm.
Andreas HAIMER summarizes: "As the inventor of Safe-Lock, HAIMER steps up and offers this shank solution as a standard for all HAIMER Power Mill tools starting from shank diameter 6mm and intentionally gives up on plain round and Weldon shanks."
Due to the inherently balanced design, the Safe-Lock shanks can be clamped in standard shrink fit and collet chucks without any problems. HAIMER target is to have high availability and replace the Weldon system in the next 10 years. Whereas Safe-Lock not only supports roughing applications, but reportedly becomes a new universal solution that continues to find more and more use during HSC applications with high helix endmills.
Related Glossary Terms
- collet
collet
Flexible-sided device that secures a tool or workpiece. Similar in function to a chuck, but can accommodate only a narrow size range. Typically provides greater gripping force and precision than a chuck. See chuck.
- endmill
endmill
Milling cutter held by its shank that cuts on its periphery and, if so configured, on its free end. Takes a variety of shapes (single- and double-end, roughing, ballnose and cup-end) and sizes (stub, medium, long and extra-long). Also comes with differing numbers of flutes.
- milling machine ( mill)
milling machine ( mill)
Runs endmills and arbor-mounted milling cutters. Features include a head with a spindle that drives the cutters; a column, knee and table that provide motion in the three Cartesian axes; and a base that supports the components and houses the cutting-fluid pump and reservoir. The work is mounted on the table and fed into the rotating cutter or endmill to accomplish the milling steps; vertical milling machines also feed endmills into the work by means of a spindle-mounted quill. Models range from small manual machines to big bed-type and duplex mills. All take one of three basic forms: vertical, horizontal or convertible horizontal/vertical. Vertical machines may be knee-type (the table is mounted on a knee that can be elevated) or bed-type (the table is securely supported and only moves horizontally). In general, horizontal machines are bigger and more powerful, while vertical machines are lighter but more versatile and easier to set up and operate.
- physical vapor deposition ( PVD)
physical vapor deposition ( PVD)
Tool-coating process performed at low temperature (500° C), compared to chemical vapor deposition (1,000° C). Employs electric field to generate necessary heat for depositing coating on a tool’s surface. See CVD, chemical vapor deposition.
- shank
shank
Main body of a tool; the portion of a drill or similar end-held tool that fits into a collet, chuck or similar mounting device.
- tolerance
tolerance
Minimum and maximum amount a workpiece dimension is allowed to vary from a set standard and still be acceptable.