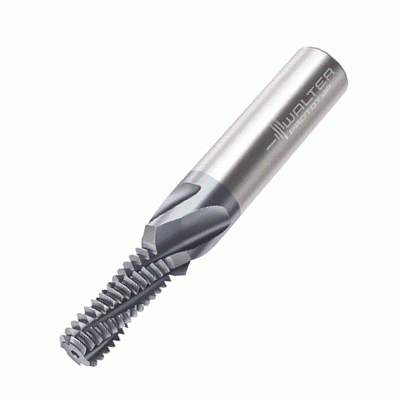
To thread a hole and countersink it in one operation, Walter USA LLC, Waukesha, Wis., (www.walter-tools.com/us) introduced a new version of the Prototyp TMC thread mill with a 90° countersink. "A lot of times it's cost-prohibitive to order a step drill, for example, or have a separate countersinking operation," said Mark Hemmerling, Walter's director of marketing.
Other enhancements include a wear-resistant and tough ultrafine-grain carbide substrate, a 27° helix with a shortened flute runout for effective chip evacuation when cutting a variety of materials, through-coolant for threads down to M4 and a multilayer TiCN coating that reportedly permits higher cutting speeds and longer tool life. The tools are also available uncoated and can produce threads from M3 to M16. The tools have an aggressive rake angle and can thread material as hard as 48 HRC.
In laboratory comparisons with similar tools, the company reported that the new TMC thread mill lasts 50 to 100 percent longer. For example, an automotive and racing company applied the tool to mill M4 threads 2 diameter deep in control arms made of 300-M steel, which has a tensile strength of 217,550 psi. With the TMC thread mill, the company achieved a 200-sfm cutting speed and 0.0007" feed per tooth and increased the number of threads cut during a set amount of time from 80 to 145—an 81 percent increase.
In another application, a contract manufacturer machining coupling flanges made of 6150 spring steel, which has a tensile strength of 152,280 psi, cut ½"-deep M10 threads with a TMC tool. Machining parameters were 220 sfm and a 0.0014" feed per tooth. The previous tool cut 120 threads during a set amount of time compared to almost 550 threads for the TMC.
The latest version of the company's TEC-CSS tool selection and cutting date software, Version 10.3, contains optimized values for the TMC thread mill with countersink. The online software is available free of charge and recommends a tool based on the application, workpiece material and its hardness. "It lets you know what tools can be used as well as the speeds and feeds, estimated tool life and estimated cost per part based on your hourly shop rate," Hemmerling said. "We launch two updates per year to coincide with new product introductions."
Contact Details
Related Glossary Terms
- countersink
countersink
Tool that cuts a sloped depression at the top of a hole to permit a screw head or other object to rest flush with the surface of the workpiece.
- countersinking
countersinking
Cutting a beveled edge at the entrance of a hole so a screw head sits flush with the workpiece surface.
- cutting speed
cutting speed
Tangential velocity on the surface of the tool or workpiece at the cutting interface. The formula for cutting speed (sfm) is tool diameter 5 0.26 5 spindle speed (rpm). The formula for feed per tooth (fpt) is table feed (ipm)/number of flutes/spindle speed (rpm). The formula for spindle speed (rpm) is cutting speed (sfm) 5 3.82/tool diameter. The formula for table feed (ipm) is feed per tooth (ftp) 5 number of tool flutes 5 spindle speed (rpm).
- feed
feed
Rate of change of position of the tool as a whole, relative to the workpiece while cutting.
- hardness
hardness
Hardness is a measure of the resistance of a material to surface indentation or abrasion. There is no absolute scale for hardness. In order to express hardness quantitatively, each type of test has its own scale, which defines hardness. Indentation hardness obtained through static methods is measured by Brinell, Rockwell, Vickers and Knoop tests. Hardness without indentation is measured by a dynamic method, known as the Scleroscope test.
- milling machine ( mill)
milling machine ( mill)
Runs endmills and arbor-mounted milling cutters. Features include a head with a spindle that drives the cutters; a column, knee and table that provide motion in the three Cartesian axes; and a base that supports the components and houses the cutting-fluid pump and reservoir. The work is mounted on the table and fed into the rotating cutter or endmill to accomplish the milling steps; vertical milling machines also feed endmills into the work by means of a spindle-mounted quill. Models range from small manual machines to big bed-type and duplex mills. All take one of three basic forms: vertical, horizontal or convertible horizontal/vertical. Vertical machines may be knee-type (the table is mounted on a knee that can be elevated) or bed-type (the table is securely supported and only moves horizontally). In general, horizontal machines are bigger and more powerful, while vertical machines are lighter but more versatile and easier to set up and operate.
- rake
rake
Angle of inclination between the face of the cutting tool and the workpiece. If the face of the tool lies in a plane through the axis of the workpiece, the tool is said to have a neutral, or zero, rake. If the inclination of the tool face makes the cutting edge more acute than when the rake angle is zero, the rake is positive. If the inclination of the tool face makes the cutting edge less acute or more blunt than when the rake angle is zero, the rake is negative.
- tensile strength
tensile strength
In tensile testing, the ratio of maximum load to original cross-sectional area. Also called ultimate strength. Compare with yield strength.
- titanium carbonitride ( TiCN)
titanium carbonitride ( TiCN)
Often used as a tool coating. See coated tools.