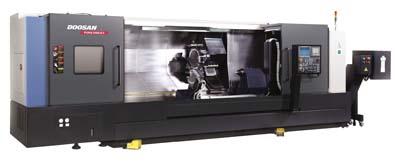
The recently introduced, Puma 3100 turning center brings new levels of speed, convenience, precision and performance to Doosan's family of high-power, horizontal turning centers. Eliminating thermal deformation is among the more notable features of the Puma 3100. Its new thermal isolation system is designed to prevent machine-generated heat from reaching the bed or headstock. Strategically placed covers deflect heat away from sensitive areas, while fans exhaust heat from the machine.
In addition, a 1.2 Hp multistage centrifugal pump delivers coolant at 65 psi which meets the criteria of most insert manufacturers. It is, also, sufficient to flush chips from drilled holes, reducing the need for peck drilling cycles. Coolant is stored in tanks ranging from 60 to 126 gallons depending on the model selected. A Presci-Flex tooling system uses a single base holder configured to accept collets, endmill holders, expanding collet chucks, shrink fit tooling, Capto and KM system tooling. A conical and flat-face planar interface assures superior accuracy and rigidity. nterchanging pre-set tools reduces downtime to a minimum.
The Puma 3100 is suitable for parts as large as 16.5" diam. x 29.9" long (a model with an elongated bed extends part length to 50.4"), and accepts bar stock to 4" diameter. A 30 Hp motor drives the spindle at speeds up to 2,800 rpm and generates a maximum spindle torque of 828 ft-lbs. A 12-staton turret selects BMT65 tools bi-directionally in 0.15 seconds. The turret is non-lifting to eliminate the possibility of contamination reaching the coupling. A 9" curvic coupling with 11,900 lbs. of hydraulic clamping force provides high rigidity for heavy stock removal, fine surface finishes, long boring bar overhang ratios, and extended tool life.
Rotating tools are powered by a 7.5 Hp motor, generating 34.7 ft-lbs of low-end torque, and speeds up to 5,000 rpm. A tool setter reduces set-up time by minimizing the need for manual skim cuts. Offsets are calculated and automatically entered into the program, eliminating clerical errors. A one-piece, fine-grain Meehanite casting inhibits thermal deformation and twisting, and dampens shock and vibration. The bed is a true 30 degree slant bed design to maintain minimal and constant distance between the tool tip and bed ways. This assures maximum rigidity and eliminates deformation under heavy loads.
Widely spaced wrap-around guideways combine speed with long-term rigidity and accuracy. Each guide way is induction hardened, precision ground, bonded with a fluroplastic resin, and hand scraped for further vibration dampening and to provide an appropriate flow of lubricant along the guide way surface. Additional standard features of the Puma 3100 include a way lube separation system, chip guarding, an 87 degree swiveling operator's panel, Fanuc embedded Ethernet function, and a tool monitoring system which monitors spindle and axis load while the axis is feeding. Both overload and underload conditions are monitored to assist in optimizing operating conditions. Also available is a programmable tailstock with a build-in live center for Y-axis models.
Models are available with Y-axis, elongated beds, and live tooling. The controller is a Fanuc 0iTD.
Contact Details
Related Glossary Terms
- boring
boring
Enlarging a hole that already has been drilled or cored. Generally, it is an operation of truing the previously drilled hole with a single-point, lathe-type tool. Boring is essentially internal turning, in that usually a single-point cutting tool forms the internal shape. Some tools are available with two cutting edges to balance cutting forces.
- boring bar
boring bar
Essentially a cantilever beam that holds one or more cutting tools in position during a boring operation. Can be held stationary and moved axially while the workpiece revolves around it, or revolved and moved axially while the workpiece is held stationary, or a combination of these actions. Installed on milling, drilling and boring machines, as well as lathes and machining centers.
- centers
centers
Cone-shaped pins that support a workpiece by one or two ends during machining. The centers fit into holes drilled in the workpiece ends. Centers that turn with the workpiece are called “live” centers; those that do not are called “dead” centers.
- collet
collet
Flexible-sided device that secures a tool or workpiece. Similar in function to a chuck, but can accommodate only a narrow size range. Typically provides greater gripping force and precision than a chuck. See chuck.
- coolant
coolant
Fluid that reduces temperature buildup at the tool/workpiece interface during machining. Normally takes the form of a liquid such as soluble or chemical mixtures (semisynthetic, synthetic) but can be pressurized air or other gas. Because of water’s ability to absorb great quantities of heat, it is widely used as a coolant and vehicle for various cutting compounds, with the water-to-compound ratio varying with the machining task. See cutting fluid; semisynthetic cutting fluid; soluble-oil cutting fluid; synthetic cutting fluid.
- endmill
endmill
Milling cutter held by its shank that cuts on its periphery and, if so configured, on its free end. Takes a variety of shapes (single- and double-end, roughing, ballnose and cup-end) and sizes (stub, medium, long and extra-long). Also comes with differing numbers of flutes.
- turning
turning
Workpiece is held in a chuck, mounted on a face plate or secured between centers and rotated while a cutting tool, normally a single-point tool, is fed into it along its periphery or across its end or face. Takes the form of straight turning (cutting along the periphery of the workpiece); taper turning (creating a taper); step turning (turning different-size diameters on the same work); chamfering (beveling an edge or shoulder); facing (cutting on an end); turning threads (usually external but can be internal); roughing (high-volume metal removal); and finishing (final light cuts). Performed on lathes, turning centers, chucking machines, automatic screw machines and similar machines.