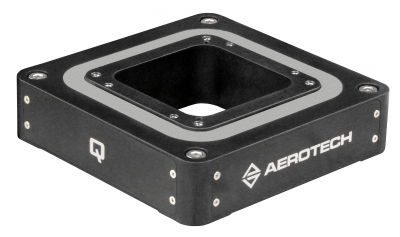
Aerotech’s QNP2 series XY, parallel-kinematic, piezo positioning stages combine subnanometer resolution, high dynamics, and excellent geometric performance in a compact, low-profile package. The QNP2-100-XYA has a 50 mm x 50 mm clear aperture with closed-loop travels up to 100 µm x 100 µm (open-loop travels to 120 µm x 120 µm). The design is ideal for optical microscopy, scanning probe microscopy, x-ray transmission microscopy, and other applications where two-sided part access is required.
QNP2 piezo stages employ a parallel-kinematic flexure and metrology design that ensures the highest level of multi-axis accuracy. FEA-optimized precision flexures ensure high-stiffness and long device life. High stiffness and resonant frequency enable exceptional process throughput and fast closed-loop response. A patent-pending drive design minimizes yaw errors while maintaining an Abbe-compliant metrology system.
All QNP2 piezo stages are available with closed-loop feedback (-C) or open-loop (no feedback). The unique capacitive sensor parallel-metrology design directly measures the output of the positioning carriage enabling 0.15 nm resolution, 0.01 percent linearity, and 1 nm bidirectional repeatability.
Aerotech’s Q-series controllers and drives provide a variety of convenient software options. The Dynamic Controls Toolbox and Motion Designer packages have a host of advanced yet easy-to-use tools such as Learning Control, Harmonic Cancellation, and Command Shaping to improve tracking errors and increase step-and-settle times. Aerotech’s controller architecture easily enables high-speed, tightly-controlled coordinated motion between piezo stages, servos, steppers, and galvos.
An optional mounting plate allows direct mounting to English or metric breadboard optical tables, and a solid tabletop is available. QNP2 piezo stages are also offered in custom materials and vacuum-prepared versions.
Contact Details
Related Glossary Terms
- metrology
metrology
Science of measurement; the principles on which precision machining, quality control and inspection are based. See precision machining, measurement.
- shaping
shaping
Using a shaper primarily to produce flat surfaces in horizontal, vertical or angular planes. It can also include the machining of curved surfaces, helixes, serrations and special work involving odd and irregular shapes. Often used for prototype or short-run manufacturing to eliminate the need for expensive special tooling or processes.
- stiffness
stiffness
1. Ability of a material or part to resist elastic deflection. 2. The rate of stress with respect to strain; the greater the stress required to produce a given strain, the stiffer the material is said to be. See dynamic stiffness; static stiffness.