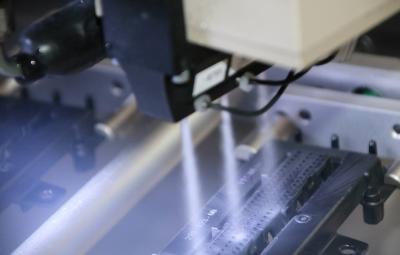
Plastic parts invariably have burrs after injection molding or mechanical processing. The quattroClean technology from acp systems AG has proved to be an efficient, inline-capable deburring and cleaning alternative for hard and brittle plastics such as PEEK and PPS. Deburring and cleaning are carried out in a single dry process.
There are practically no limits to the use of plastics today. From medical technology through automotive engineering and electronics to household and leisure products, polymer all-rounders enable innovative solutions.
However, regardless of whether components are injection-molded or mechanically processed, there are residues on the surface that have to be removed for high-quality further processing or to ensure that workpieces and components function perfectly. When it comes to burrs and residues from processing media, the quattroClean technology from acp systems AG is an effective and efficient deburring and cleaning alternative for hard and brittle plastics such as polyphenylene sulfide (PPS) and polyetheretherketone (PEEK).
Environmentally-friendly, effective and dry processing step The modular quattroClean system works with liquid carbon dioxide, which has a virtually unlimited shelf life and is generated as a by-product from chemical processes as well as energy generation from biomass. CO2 is therefore an environmentally neutral, non-flammable and non-toxic gas.
For the deburring and cleaning process, the carbon dioxide is fed through the non-wearing two-component ring nozzle of the quattroClean system, expanding as it exits to form fine CO2 snow. This is then bundled by a jacketed jet of compressed air and accelerated to supersonic speed. When the non-abrasive jet of snow and compressed air impacts at a temperature of minus 78.5° C onto the surface to be processed, a combination of thermal, mechanical, sublimation and solvent effects take place.
The thermal effect is partially responsible for the deburring action. Shock cooling causes the burrs to become brittle. In addition, the volume of the CO2 snow increases about 600 times as it changes from a solid to a gaseous state, thus creating micro-pressure waves that spread at high speed. The resulting force is sufficient to remove the burrs from the components.
Combined, the four mechanisms of action also have an efficient and homogeneous cleaning effect. They remove particulate contaminants, e.g. burrs, dust and particles, equally reliably and consistently as filmic contaminants such as residues of separating agents and silicons. The deburring and cleaning process is so gentle on materials that it can even be used to clean delicate and finely-structured surfaces.
Detached burrs and contaminants are removed from the component surface by the aerodynamic force of the compressed air and transported away by a suction unit integrated into the processing cell. Since CO2 sublimates instantly under atmospheric pressure, the components are dry at the end of the cleaning step and can be further processed or packaged straightaway.
Cost-effective solution - also for production integration The scalable quattroClean process can be efficiently and space-savingly adapted to different component geometries to enable partial or full-surface processing. Through trials in the acp systems technical center, the process parameters, such as volume flows for compressed air and carbon dioxide, jet zone and time, are precisely tailored to the respective application. These also account for the material properties and the burrs and contamination to be removed. These parameters can be filed as part-specific cleaning programs in the system control.
Tailored to the respective deburring, cleanliness and cycle time specifications, acp systems develops customized plant concepts based on standard modules, which can be operated as stand-alone solutions, or integrated into the production line or networked production environment.
The latter is made possible by the quattroClean system's industry 4.0 capability. The system can be easily integrated into and controlled by higher-level master computers via standardized interfaces. To ensure full documentation and traceability, all process parameters are automatically recorded and transferred to the host computer.