Contact Details
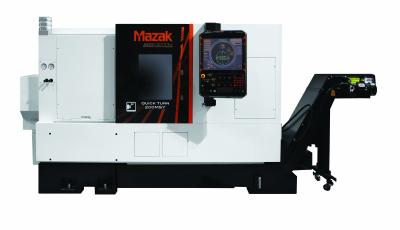
Mazak’s Quick Turn-200MSY turning center combines several features that allow shops to boost productivity and profitability. These include a direct servo-driven turret design, integral motor main and second spindle design, a faster, more powerful milling spindle and Mazak’s Mazatrol SmoothG CNC.
The Quick Turn-200MSY – with multitasking functionality – has two turning spindles, a rotary tool milling spindle and Y-axis capabilities for single setup Done In One precision part processing operations. The machine’s optional 16-position, direct servo-driven turret eliminates the use of belts for increased rpm, improved part surface finishes, reduced maintenance and more total tool holders to support complex part features. It accepts either VDI or bolt-on tooling.
The turret’s direct-drive rotary tool spindle is 10-hp, 6,000-rpm standard. This faster rotary spindle provides 35 ft.-lbs. of torque, and with an optional tooling package, 10,000 rpm is available.
The machine’s headstock features an 8" main chuck capacity on a 35-hp, 5,000-rpm integrated spindle motor for heavy-duty metal removal. The main turning spindle also serves as a C-axis that is programmable in 0.0001-degree increments to accurately position parts for square facing, milling flats, slotting cuts and precisely drilled holes. A second 10-hp, 6,000-rpm turning spindle that performs automatic workpiece transfer for secondary operations and accommodates a 6" chuck allows the Quick Turn-200MSY to machine small diameter workpieces with speed and accuracy.
Paired with Mazak’s Mazatrol SmoothG CNC, the machine offers EIA/ISO programming, as well as conversational programming, that makes it easy to generate programs for complex drilling, milling or tapping operations. The control also features advanced hardware and software functions that help ensure high productivity and performance accuracy in challenging part production operations.
For improved spindle utilization and a significant boost in overall productivity, a variety of automation strategies integrate with the Quick Turn-200MSY, from an automatic bar feeder with parts catcher system to factory integrated gantry robot.
Related Glossary Terms
- chuck
chuck
Workholding device that affixes to a mill, lathe or drill-press spindle. It holds a tool or workpiece by one end, allowing it to be rotated. May also be fitted to the machine table to hold a workpiece. Two or more adjustable jaws actually hold the tool or part. May be actuated manually, pneumatically, hydraulically or electrically. See collet.
- computer numerical control ( CNC)
computer numerical control ( CNC)
Microprocessor-based controller dedicated to a machine tool that permits the creation or modification of parts. Programmed numerical control activates the machine’s servos and spindle drives and controls the various machining operations. See DNC, direct numerical control; NC, numerical control.
- conversational programming
conversational programming
Method for using plain English to produce G-code file without knowing G-code in order to program CNC machines.
- gang cutting ( milling)
gang cutting ( milling)
Machining with several cutters mounted on a single arbor, generally for simultaneous cutting.
- gantry robot
gantry robot
Robot positioned by means of an overhead supporting structure such as a crane or bridge-type support.
- milling
milling
Machining operation in which metal or other material is removed by applying power to a rotating cutter. In vertical milling, the cutting tool is mounted vertically on the spindle. In horizontal milling, the cutting tool is mounted horizontally, either directly on the spindle or on an arbor. Horizontal milling is further broken down into conventional milling, where the cutter rotates opposite the direction of feed, or “up” into the workpiece; and climb milling, where the cutter rotates in the direction of feed, or “down” into the workpiece. Milling operations include plane or surface milling, endmilling, facemilling, angle milling, form milling and profiling.
- slotting
slotting
Machining, normally milling, that creates slots, grooves and similar recesses in workpieces, including T-slots and dovetails.
- tapping
tapping
Machining operation in which a tap, with teeth on its periphery, cuts internal threads in a predrilled hole having a smaller diameter than the tap diameter. Threads are formed by a combined rotary and axial-relative motion between tap and workpiece. See tap.
- turning
turning
Workpiece is held in a chuck, mounted on a face plate or secured between centers and rotated while a cutting tool, normally a single-point tool, is fed into it along its periphery or across its end or face. Takes the form of straight turning (cutting along the periphery of the workpiece); taper turning (creating a taper); step turning (turning different-size diameters on the same work); chamfering (beveling an edge or shoulder); facing (cutting on an end); turning threads (usually external but can be internal); roughing (high-volume metal removal); and finishing (final light cuts). Performed on lathes, turning centers, chucking machines, automatic screw machines and similar machines.