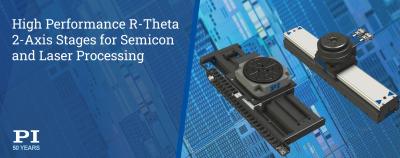
R-Theta stage motion systems are better suited to circular, elliptic and spiral motion patterns than conventional Cartesian 2-axis XY linear translation stages.
PI offers three classes of R-Theta stages.
- For the highest performance and precision, Air Bearing linear stages and air bearing rotary tables are used.
- Hybrid R-Theta systems use linear motor driven stages with mechanical bearings and direct-drive air bearing rotary tables.
- Direct Drive linear motor stages and direct drive rotary tables with mechanical bearings are also available.
R-Theta systems often find applications in precision laser / semiconductor applications due to higher throughput, higher precision and smaller footprint.
High Speed Motion Controllers
The stages are operated by PI’s ACS-based industrial motion controllers with ultra-fast triggers for synchronization with external equipment such as cameras, sensors or lasers. The fast controllers allow highly precise triggering with 0.01% time tolerance between signals. Trigger signals can be derived off absolute encoders or analog signals (sin/cos encoder), enabling higher precision, safer, and simplified solutions as compared to outdated digital encoder-only triggers. With the modern PI motion controllers, a trigger in an R-Theta configured system will work just as well as an XY position trigger, with the coordinate specifications simply defined in polar coordinates.
Contact Details
Related Glossary Terms
- linear motor
linear motor
Functionally the same as a rotary motor in a machine tool, a linear motor can be thought of as a standard permanent-magnet, rotary-style motor slit axially to the center and then peeled back and laid flat. The major advantage of using a linear motor to drive the axis motion is that it eliminates the inefficiency and mechanical variance caused by the ballscrew assembly system used in most CNC machines.
- tolerance
tolerance
Minimum and maximum amount a workpiece dimension is allowed to vary from a set standard and still be acceptable.