Contact Details
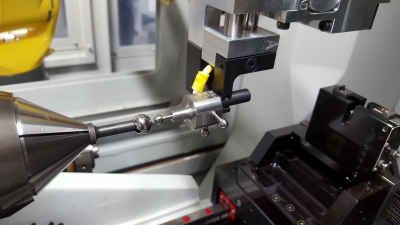
ANCA’s new RoboTeach solution enables greater efficiency and accuracy when setting up robot automation on their CNC grinding machines. By automating the teaching of the RoboMate FANUC 200iD robot, the new product significantly decreases downtime, supports greater productivity, and reduces the need for specialized operator skills. Robot teaching time can be reduced from several hours to less than 30 minutes.
Simon Richardson, ANCA MX machine platform product manager, said, “Until now, teaching of the FANUC robot (200iD) on RoboMate could be labor intensive and require a unique set of operator skills. Furthermore, accuracy could vary depending on the user conducting the teaching. To solve this problem, ANCA has released RoboTeach, a software product that automates the teaching of the RoboMate FANUC 200iD robots on our MX and TX machine platforms.”
RoboTeach promotes consistent teaching of the robot, contributing to improved grinding accuracy and better grinding cycle times, according to the company.
RoboTeach is a machine-run program that uses the high accuracy of the grinding machine to measure the robot position and automatically teach and calibrate robot positioning. The teaching process uses an electrical contact touch probe held in the robot gripper and a mandrel that locates the position of the machine collet adaptor and tool storage pallets.
A series of instructions on the operator screen guide the user on how to teach the FANUC robot using ANCA Loadermate software. The easy-to-follow instructions ensure the operator can quickly and easily teach the robot positions and coordinates.
The RoboTeach product has a software option and teach tooling kit. The teach tooling kit is supplied in a compact carry case with relevant teaching materials.
Related Glossary Terms
- collet
collet
Flexible-sided device that secures a tool or workpiece. Similar in function to a chuck, but can accommodate only a narrow size range. Typically provides greater gripping force and precision than a chuck. See chuck.
- computer numerical control ( CNC)
computer numerical control ( CNC)
Microprocessor-based controller dedicated to a machine tool that permits the creation or modification of parts. Programmed numerical control activates the machine’s servos and spindle drives and controls the various machining operations. See DNC, direct numerical control; NC, numerical control.
- grinding
grinding
Machining operation in which material is removed from the workpiece by a powered abrasive wheel, stone, belt, paste, sheet, compound, slurry, etc. Takes various forms: surface grinding (creates flat and/or squared surfaces); cylindrical grinding (for external cylindrical and tapered shapes, fillets, undercuts, etc.); centerless grinding; chamfering; thread and form grinding; tool and cutter grinding; offhand grinding; lapping and polishing (grinding with extremely fine grits to create ultrasmooth surfaces); honing; and disc grinding.
- grinding machine
grinding machine
Powers a grinding wheel or other abrasive tool for the purpose of removing metal and finishing workpieces to close tolerances. Provides smooth, square, parallel and accurate workpiece surfaces. When ultrasmooth surfaces and finishes on the order of microns are required, lapping and honing machines (precision grinders that run abrasives with extremely fine, uniform grits) are used. In its “finishing” role, the grinder is perhaps the most widely used machine tool. Various styles are available: bench and pedestal grinders for sharpening lathe bits and drills; surface grinders for producing square, parallel, smooth and accurate parts; cylindrical and centerless grinders; center-hole grinders; form grinders; facemill and endmill grinders; gear-cutting grinders; jig grinders; abrasive belt (backstand, swing-frame, belt-roll) grinders; tool and cutter grinders for sharpening and resharpening cutting tools; carbide grinders; hand-held die grinders; and abrasive cutoff saws.
- mandrel
mandrel
Workholder for turning that fits inside hollow workpieces. Types available include expanding, pin and threaded.