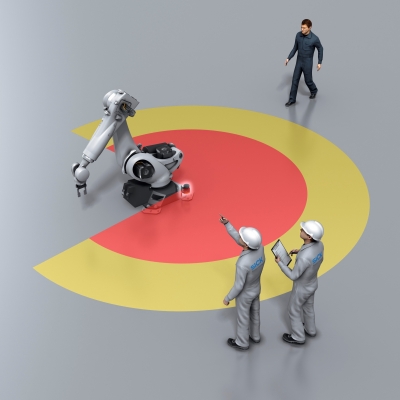
The Safe Robotics Area Protection (SRAP) safety system from SICK provides process-based protection for collaborative robot applications.
The safety system provides machine operators with unrestricted, yet safe, access to a robot’s working area at any time, by adapting the operating conditions to the position of the person. These adaptive perception capabilities prevent the risk of accidents from occurring and simultaneously improve productivity. It reduces downtime and optimizes the ergonomic and process aspects of the operator’s workflow.
The SRAP system consists of a Flexi Soft safety controller and a safety laser scanner – either the space-saving S300 Mini Remote for shorter scanning ranges or the microScan3 Core for larger monitoring fields. Safe Robotics Area Protection satisfies the criteria of Performance Level PL d in accordance with EN ISO 13849-1.
SRAP is a complete turnkey solution that is ready to use in no time at all. With prefabricated and tested software function blocks, the safety system can be integrated with ease and fits seamlessly into the controllers of all standard industrial robots.
The migration capabilities of the system configuration, plus the option of adapting it in line with additional safety functions, make Safe Robotics Area Protection a future-proof safety system that enables flexible, autonomous machines and robots to adapt quickly and effortlessly to new production conditions, safety requirements and protective field conditions that result from this.
SRAP intelligently combines the functions of a safety laser scanner – either the S300 Mini Remote or the microScan3 Core – with the possibilities offered by the Flexi Soft safety controller. This means that, based on the monitoring situation at the robot, differently dimensioned field sets can be equipped with warning and protective functions in the laser scanners and dynamically adapted in line with a detected worker position.
Depending on how close the person is to the robot, the sensors cause the robot’s movement to either reduce or stop via the Flexi Soft safety controller – so that workpieces can be inserted or removed, for example. If the person then leaves the monitored area, the safety system automatically starts performing sequence monitoring.
Provided that this monitoring satisfies the requirements for operating the robot safely, the robot is first started up at a reduced speed and then returns to its original working speed once all the warning and protective fields are free again. This means that the worker remains constantly protected against hazardous movements whenever they enter the robot’s working area.
At the same time, the automated restart reduces downtime once a worker leaves the hazardous area, and also optimizes the worker’s processes – laying the foundations for machines and industrial robots to be more productive.
The SRAP safety system offers versatility. It makes it possible to factor in new working situations and conditions, and take account of non-safe automation functions and safety-related functions being carried out simultaneously – in the way that they have been prefabricated and tested.
In turn, this allows the safety system to be integrated into the most commonly used varieties of robot controllers with minimum integration work, using the function block provided. If other safety devices are added or additional safety functions become necessary during operation, these can be integrated with ease later on – making the SRAP safety system even more of a sound, future-proof investment.
Contact Details
Related Glossary Terms
- robotics
robotics
Discipline involving self-actuating and self-operating devices. Robots frequently imitate human capabilities, including the ability to manipulate physical objects while evaluating and reacting appropriately to various stimuli. See industrial robot; robot.