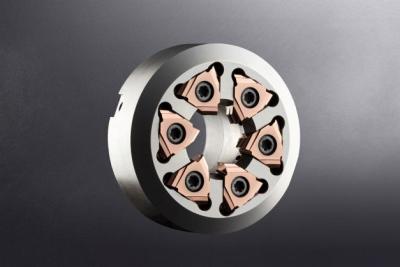
SG3P is the name of the newly developed Horn high-performance grade offering the user new possibilities in terms of performance and tool life when whirling medical screws.
The new carbide grade also enables shorter cycle times for thread production thanks to higher cutting values, including when processing materials that are difficult to machine. In addition, the combination of an ultra-fine grain carbide powder and the high temperature resistant coating results in high process reliability and better component quality. The carbide grade is available for all standard Horn thread whirling systems. Furthermore, in-house coating enables fast delivery times.
The production of bone screws must necessarily be carried out using a metalcutting process, as the material for this type of screw must not be compressed, as is the case with thread rolling, for example. Titanium in particular, which is mainly used in the human body because of its good biocompatibility, tends to burn if the material is compressed too much. As a machining process, thread whirling has been established for many years.
Conventional thread whirling is a process that is mainly used on Swiss-type lathes to manufacture bone screws, but also on a larger scale for the production of threaded spindles. In the process, the rapidly-rotating whirling head is positioned eccentrically to the workpiece axis in front of the guide bush of the sliding-headstock lathe and the slowly rotating workpiece is guided into the whirling head with an axial feed movement.
Contact Details
Related Glossary Terms
- feed
feed
Rate of change of position of the tool as a whole, relative to the workpiece while cutting.
- lapping compound( powder)
lapping compound( powder)
Light, abrasive material used for finishing a surface.
- lathe
lathe
Turning machine capable of sawing, milling, grinding, gear-cutting, drilling, reaming, boring, threading, facing, chamfering, grooving, knurling, spinning, parting, necking, taper-cutting, and cam- and eccentric-cutting, as well as step- and straight-turning. Comes in a variety of forms, ranging from manual to semiautomatic to fully automatic, with major types being engine lathes, turning and contouring lathes, turret lathes and numerical-control lathes. The engine lathe consists of a headstock and spindle, tailstock, bed, carriage (complete with apron) and cross slides. Features include gear- (speed) and feed-selector levers, toolpost, compound rest, lead screw and reversing lead screw, threading dial and rapid-traverse lever. Special lathe types include through-the-spindle, camshaft and crankshaft, brake drum and rotor, spinning and gun-barrel machines. Toolroom and bench lathes are used for precision work; the former for tool-and-die work and similar tasks, the latter for small workpieces (instruments, watches), normally without a power feed. Models are typically designated according to their “swing,” or the largest-diameter workpiece that can be rotated; bed length, or the distance between centers; and horsepower generated. See turning machine.
- metalcutting ( material cutting)
metalcutting ( material cutting)
Any machining process used to part metal or other material or give a workpiece a new configuration. Conventionally applies to machining operations in which a cutting tool mechanically removes material in the form of chips; applies to any process in which metal or material is removed to create new shapes. See metalforming.
- thread rolling
thread rolling
Chipless, cold-forming material-displacement process where a rolling head is pressed into the workpiece to create threads. The material is stressed beyond its yield point, which causes it to be deformed platically and permanently. There are three basic types of rolling heads: axial, radial and tangential.