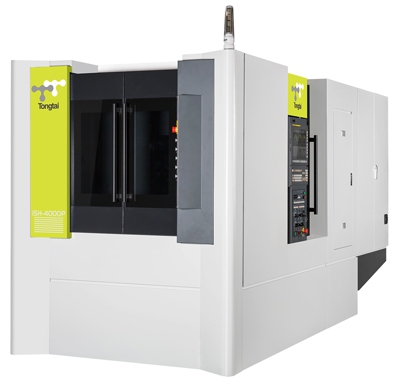
The new SH-4000 horizontal machining center from Tongtai, distributed by Absolute Machine Tools Inc., was developed for mass production line formation and fast aluminum alloy parts machining. The new compact machine has a 35 percent smaller footprint than the previous model, allowing for maximum shop floor utilization throughput. By integrating a robot on either a floor-type motion axis rail system or overhead gantry, manufacturers are able to catapult production and streamline manpower costs.
Tongtai's SH-4000 is equipped with a powerful 30HP, 15K RPM built-in spindle, 400mm square table, and coolant through the spindle. The automatic tool changer can hold 60 tools with a tool- to-tool change time of 1.4 seconds, and chip-to-chip time of 2.6 seconds. The cam-type automatic pallet changer has a change time of 6.0 seconds. The SH-4000 comes standard with linear ways for speed and with optional linear scales for achieving accuracy of ±3 µm. Travels for X/Y/Z are 510mm each with rapid traverse rates of 60m/minute on each axes, accelerating at a rate of 1.0-G. The B-axis rotary table can index at 0.001° with or without an encoder. Because the B-axis is made with a roller gear cam mechanism, it is much more durable than a worm gear type, guarantees higher accuracy, and is preloaded for zero backlash.
Tongtai's Flexible Manufacturing System, or FMS, is recommended with this model for increased finished parts volume. The FMS consists of a loading/unloading station, stacker crane, pallet container, and Manufacturing Management System (MMS) monitoring. This system is dedicated specifically for the horizontal SH-4000. It begins at the loading/unloading station where raw materials are initiated into the FMS and ends as a finished part. FMS can handle up to two loading/unloading stations per cell. Next, the part moves on a pallet from the loading station to the stacker crane where it gets loaded and ultimately unloaded in the machine(s). The pallet container allows for temporary storage of the raw materials heading to the stacker, and finished materials from the stacker back to the unloading station, or to additional machines for finishing. The container system in the FMS can have as many as 10 pallets, or be expanded to a maximum of 20. A Manufacturing Management System (MMS) is used to program the FMS and monitors the movement and machining of the entire system by collecting the production information for the operator. Tongtai's FMS is extremely flexible and each of the cell's stations is built to coordinate with each other.
Tongtai's Intelligent Manufacturing System (TIMS) is among the newest technologies in the machine tool industry. Developed by Tongtai and partnering with FANUC, this system includes four basic management functions for any size manufacturing facility to improve productivity, machine accurately and precisely, facilitate part production, as well as provide protection and maintenance assistance for the machine tool. The Production Management System monitors cutting loads, pallet-changing functions, records alarm messages, and assists in troubleshooting and maintenance support. The Intelligent Management System performs motor load monitoring, machining adaptive controls for protecting tooling and ensuring cutting efficiency, and crash protection for real time detection of servo loads during feeding. Tool Management records machining dates, times, and usage for tool life tracking and management, tool compensation, and tool overload protection. The fourth management function is Workpiece Management. This function incorporates software using a built-in CCD camera to monitor the characteristics of a particular workpiece, and calculates and compensates program coordinates for maximizing machining precision.
Contact Details
Related Glossary Terms
- backlash
backlash
Reaction in dynamic motion systems where potential energy that was created while the object was in motion is released when the object stops. Release of this potential energy or inertia causes the device to quickly snap backward relative to the last direction of motion. Backlash can cause a system’s final resting position to be different from what was intended and from where the control system intended to stop the device.
- computer-aided manufacturing ( CAM)
computer-aided manufacturing ( CAM)
Use of computers to control machining and manufacturing processes.
- coolant
coolant
Fluid that reduces temperature buildup at the tool/workpiece interface during machining. Normally takes the form of a liquid such as soluble or chemical mixtures (semisynthetic, synthetic) but can be pressurized air or other gas. Because of water’s ability to absorb great quantities of heat, it is widely used as a coolant and vehicle for various cutting compounds, with the water-to-compound ratio varying with the machining task. See cutting fluid; semisynthetic cutting fluid; soluble-oil cutting fluid; synthetic cutting fluid.
- flexible manufacturing system ( FMS)
flexible manufacturing system ( FMS)
Automated manufacturing system designed to machine a variety of similar parts. System is designed to minimize production changeover time. Computers link machine tools with the workhandling system and peripherals. Also associated with machine tools grouped in cells for efficient production. See cell manufacturing.
- flexible manufacturing system ( FMS)2
flexible manufacturing system ( FMS)
Automated manufacturing system designed to machine a variety of similar parts. System is designed to minimize production changeover time. Computers link machine tools with the workhandling system and peripherals. Also associated with machine tools grouped in cells for efficient production. See cell manufacturing.
- machining center
machining center
CNC machine tool capable of drilling, reaming, tapping, milling and boring. Normally comes with an automatic toolchanger. See automatic toolchanger.
- rapid traverse
rapid traverse
Movement on a CNC mill or lathe that is from point to point at full speed but, usually, without linear interpolation.