Contact Details
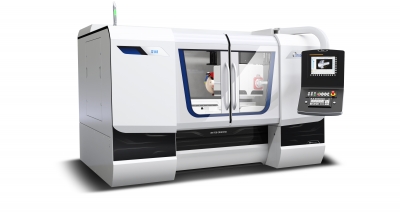
To ensure manufacturers can obtain the most productive machine for their particular part-production applications, United Grinding offers a full 360-degree range of Studer internal cylindrical grinding machines. This extensive portfolio of machines includes several universal-type models, as well as those designed for high production and for radii grinding operations.
In the universal range are the Studer S121, S131, S141 (pictured) and S151 models for workpieces up to 1,300 mm long and weighing as much as 250 kg. The cost-effective universal S121 is well-suited for internal, surface and external grinding of chuck components, while the S131, S141 and S151 handle all other conceivable internal cylindrical grinding applications. The machines deliver the highest precision and efficiency, especially for flange parts, spindle shafts, spindle housings, rotor shafts and bushings.
Ideal for chuck applications involving one component up to small-batch production, the Studer S110 is a flexible and compact internal cylindrical grinding machine designed for shops with limited floor space. For small to large-scale production, the Studer S122 specializes in small-bore grinding and has a swing diameter of 220 mm. Both machines can have up to three grinding spindles in a parallel arrangement that allows for external and internal grinding in a single clamping.
Three Studer models, the S121, S131 and S141, specialize in high-precision internal cylindrical grinding of radii, spheres, balls, cones and diameters. This range of machines accommodates maximum swing diameters up to 400 mm and workpiece weights up to 100 kg. Applications include the manufacture of die plates from carbide and ceramic, as well as the production of hydraulic components such as axial pump pistons, guide plates and housings from hardened steel, cast iron and copper. These machines are also well-suited for workpieces made from industrial ceramic, sapphire and carbide materials frequently used in the manufacture of human surgical implants. StuderSIM software supports the automatic direct drive B-axes of the Studer S121, S131 and S141, which allows these machines to interpolate for high-precision radii grinding.
The StuderSIM software has been specially developed for the internal grinding of radii. The operating system enables programming of all basic cycles for grinding, dressing and process-supporting measurement. This type of programming guarantees high flexibility together with maximum user-friendliness. After programming, the process can be simulated and optimized to ensure reliability, as well as shorten programming times and boost cost effectiveness.
For simplifying other complex internal cylindrical grinding operations, StuderWIN software allows for the full integration of in-process gauging and sensor technology for process monitoring, including contact detection and automatic balancing systems within the operator interface for standardized programming across different systems. StuderWIN is further supplemented with StuderPictogramming grinding software, which gives operators the ability to string individual grinding cycles together into ISO code generated by the control unit. The machine's functionality is enhanced by the software option for thread and form grinding.
Related Glossary Terms
- chuck
chuck
Workholding device that affixes to a mill, lathe or drill-press spindle. It holds a tool or workpiece by one end, allowing it to be rotated. May also be fitted to the machine table to hold a workpiece. Two or more adjustable jaws actually hold the tool or part. May be actuated manually, pneumatically, hydraulically or electrically. See collet.
- cylindrical grinding
cylindrical grinding
Grinding operation in which the workpiece is rotated around a fixed axis while the grinding wheel is fed into the outside surface in controlled relation to the axis of rotation. The workpiece is usually cylindrical, but it may be tapered or curvilinear in profile. See centerless grinding; grinding.
- dressing
dressing
Removal of undesirable materials from “loaded” grinding wheels using a single- or multi-point diamond or other tool. The process also exposes unused, sharp abrasive points. See loading; truing.
- grinding
grinding
Machining operation in which material is removed from the workpiece by a powered abrasive wheel, stone, belt, paste, sheet, compound, slurry, etc. Takes various forms: surface grinding (creates flat and/or squared surfaces); cylindrical grinding (for external cylindrical and tapered shapes, fillets, undercuts, etc.); centerless grinding; chamfering; thread and form grinding; tool and cutter grinding; offhand grinding; lapping and polishing (grinding with extremely fine grits to create ultrasmooth surfaces); honing; and disc grinding.
- grinding machine
grinding machine
Powers a grinding wheel or other abrasive tool for the purpose of removing metal and finishing workpieces to close tolerances. Provides smooth, square, parallel and accurate workpiece surfaces. When ultrasmooth surfaces and finishes on the order of microns are required, lapping and honing machines (precision grinders that run abrasives with extremely fine, uniform grits) are used. In its “finishing” role, the grinder is perhaps the most widely used machine tool. Various styles are available: bench and pedestal grinders for sharpening lathe bits and drills; surface grinders for producing square, parallel, smooth and accurate parts; cylindrical and centerless grinders; center-hole grinders; form grinders; facemill and endmill grinders; gear-cutting grinders; jig grinders; abrasive belt (backstand, swing-frame, belt-roll) grinders; tool and cutter grinders for sharpening and resharpening cutting tools; carbide grinders; hand-held die grinders; and abrasive cutoff saws.
- parallel
parallel
Strip or block of precision-ground stock used to elevate a workpiece, while keeping it parallel to the worktable, to prevent cutter/table contact.
Additional Products from United Grinding North America Inc.
Pagination
- First page
- Previous page
- 1
- 2
- 3
- 4
- 5