Contact Details
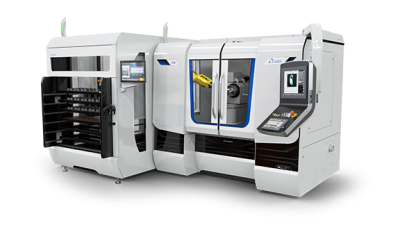
With the introduction of the new STUDER roboLoad system, UNITED GRINDING now offers manufacturers simple, seamless part-loading automation for CNC radius internal grinding machines such as the company’s STUDER S121, S131 and S141. Until now, loader integration was intrinsically difficult on these types of machines because of the height of their workheads and associated geometric restrictions. The new STUDER loader not only meets the geometrical requirements but also has a comparatively small footprint and an exceptional price-performance ratio. For even more ease of use, it operates without any programming knowledge, allowing for greater production flexibility and a high degree of operating comfort.
On the STUDER S121, S131, and S141 machines – often used to produce dies for the packaging industry – automatic B axes swivel in a range from -60° to +91°. That, according to Daniel Schafroth, Systems Division Manager at STUDER, is why any automation must be able to exit the machine and give the B axis the freedom to swivel. The STUDER roboLoadoffers that capability.
As an external loader, STUDER roboLoad measures only 59.06" (1.50 m) wide: half the width of the machine itself. This saves valuable shop floor space, and yet the system offers plenty of room for workpieces manually loaded on six trays – each measuring 42.52" x 12.6” (1080 mm x 320 mm) – within a comparatively small work area.
"We are not talking about large-scale production, but instead unmanned production during the night shift, for example, or making optimum use of breaks in other production processes," explained Schafroth. Operators can bring up any grinding program for the workpieces, and the STUDER roboLoad processes them and places each workpiece back in the same place after machining.
For simplicity of operation, the STUDER roboLoad incorporates a setup wizard developed by automation specialists from WENGER of Winterthur, Switzerland. It requires no programming knowledge on the part of the setter or machine operator. "The easy-to-follow steps are graphically presented on a large 19'' intuitive display," explained Managing Director Michael Wenger.
"We have had a successful development partnership with WENGER for 25 years," said Schafroth. The goal was that an operator should be able to set up a new workpiece, including the changeover of the gripper jaws, within 15 minutes. "And we succeeded," Wenger said.
STUDER roboLoad Specifications:
- Robot: Fanuc M10-iD 10L
- Siemens Simotion Control
- Grippers with quick-change jaws, convertible to:
- Single gripper for parts weighing up to 15.4 lbs (7 kg) or
- Dual gripper for parts weighing up to 6.2 lbs (2.8 kg)
- Maximum workpiece size:
- Diameter: 10.24” (260 mm)
- Length: 0.39"-3.93” (10-100 mm)
- Workpiece storage: 6 trays, each 42.52 x 12.6” (1080 x 320 mm)
- Intuitive 19’’ touch control panel
Related Glossary Terms
- computer numerical control ( CNC)
computer numerical control ( CNC)
Microprocessor-based controller dedicated to a machine tool that permits the creation or modification of parts. Programmed numerical control activates the machine’s servos and spindle drives and controls the various machining operations. See DNC, direct numerical control; NC, numerical control.
- grinding
grinding
Machining operation in which material is removed from the workpiece by a powered abrasive wheel, stone, belt, paste, sheet, compound, slurry, etc. Takes various forms: surface grinding (creates flat and/or squared surfaces); cylindrical grinding (for external cylindrical and tapered shapes, fillets, undercuts, etc.); centerless grinding; chamfering; thread and form grinding; tool and cutter grinding; offhand grinding; lapping and polishing (grinding with extremely fine grits to create ultrasmooth surfaces); honing; and disc grinding.
Additional Products from United Grinding North America Inc.
Pagination
- First page
- Previous page
- 1
- 2
- 3
- 4
- 5