Contact Details
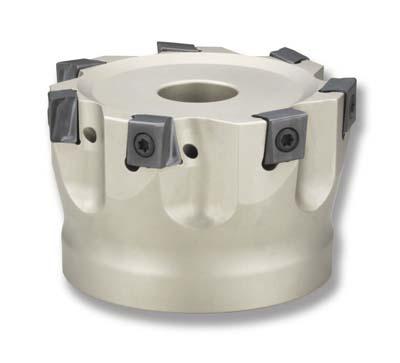
To improve productivity and reduce tooling costs, Tungaloy America has introduced the new TecMill series of shoulder milling cutters. The TecMill incorporates Tungaloy technology to give the end user increased feed rates and efficient cutting to deliver reduced tooling costs and generous productivity improvements, according to the company. The TecMill features the company's unique tangential clamping that works in harmony with a thicker core design that improves insert and cutter body strength, a combination that reduces body deformation to improve cutter performance. The TecMill is for high-speed and high-feed machining and the strength of the cutter body reportedly improves cutting edge toughness, rigidity and increases metal-removal rates by more than 30 percent. The TecMill is available as a shell or shank type cutter. The shell-type cutter has a close or coarse-pitch option with the close pitch cutter having a 9 to 11 insert option, while the coarse pitch cutter body is available with anything from 5 to 7 inserts. The coarse shell-type cutter is available with 2.0"-, 2.50"-, 3.0"-, 4.0"- and 6.0"-dia. capacities and the close pitch cutting head has an 3.0"- and 4.0"-dia. option, both pitch types are available with air holes. The shank-style TecMill has two possible options with 3 and 4 insert pocket heads, offering 1.25" and 1.50" cutting diameters at an overall cutter length of 4.0". This new series has an extremely diverse machining range that enables it to machine gray and ductile iron, low- and high-carbon steel, alloy and tool steel and heat-resistant alloys. Machining materials beyond a hardness level of 300 HB at cutting speeds of 750 SFM and feed rates of 0.012 ipt, the TecMill has a diverse machining range that is accompanied by Tungaloy's AH725, AH140 and AH120 insert grades.
Related Glossary Terms
- Brinell hardness number ( HB)
Brinell hardness number ( HB)
Number related to the applied load (usually, 500 kgf and 3,000 kgf) and to the surface area of the permanent impression made by a 10mm ball indenter. The Brinell hardness number is a calculated value of the applied load (kgf) divided by the surface area of the indentation (mm2). Therefore, the unit of measure of a Brinell hardness number is kgf/mm2, but it is always omitted.
- alloys
alloys
Substances having metallic properties and being composed of two or more chemical elements of which at least one is a metal.
- feed
feed
Rate of change of position of the tool as a whole, relative to the workpiece while cutting.
- gang cutting ( milling)
gang cutting ( milling)
Machining with several cutters mounted on a single arbor, generally for simultaneous cutting.
- hardness
hardness
Hardness is a measure of the resistance of a material to surface indentation or abrasion. There is no absolute scale for hardness. In order to express hardness quantitatively, each type of test has its own scale, which defines hardness. Indentation hardness obtained through static methods is measured by Brinell, Rockwell, Vickers and Knoop tests. Hardness without indentation is measured by a dynamic method, known as the Scleroscope test.
- inches per tooth ( ipt)
inches per tooth ( ipt)
Linear distance traveled by the cutter during the engagement of one tooth. Although the milling cutter is a multi-edge tool, it is the capacity of each individual cutting edge that sets the limit of the tool, defined as: ipt = ipm/number of effective teeth 5 rpm or ipt = ipr/number of effective teeth. Sometimes referred to as the chip load.
- milling
milling
Machining operation in which metal or other material is removed by applying power to a rotating cutter. In vertical milling, the cutting tool is mounted vertically on the spindle. In horizontal milling, the cutting tool is mounted horizontally, either directly on the spindle or on an arbor. Horizontal milling is further broken down into conventional milling, where the cutter rotates opposite the direction of feed, or “up” into the workpiece; and climb milling, where the cutter rotates in the direction of feed, or “down” into the workpiece. Milling operations include plane or surface milling, endmilling, facemilling, angle milling, form milling and profiling.
- pitch
pitch
1. On a saw blade, the number of teeth per inch. 2. In threading, the number of threads per inch.
- shank
shank
Main body of a tool; the portion of a drill or similar end-held tool that fits into a collet, chuck or similar mounting device.