Contact Details
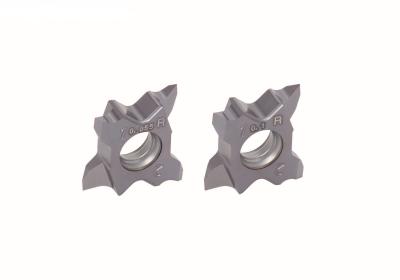
Tungaloy Corp. added threading inserts with sharp cutting edges to its TetraMini-Cut insert series, which allows undercutting and finishing of a flange wall. Complemented by the new PVD grade, SH725, TetraMini-Cut’s new threading insert features sharp cutting edges, making it suitable for cutting fine pitch threads at a high cutting speed. The cutting edge is offset to one side of the insert, allowing threading all the way to the flange wall.
The threading inserts of the TetraMini-Cut series are ground finished making them an ideal choice when high accuracy and quality are required in a threading operation. The innovative insert pocket shelters unused cutting edges from chip damages, assuring the full usage of all four cutting edges. Tungaloy’s unique clamping system secures insert rigidity and guarantees accurate repeatability.
Related Glossary Terms
- cutting speed
cutting speed
Tangential velocity on the surface of the tool or workpiece at the cutting interface. The formula for cutting speed (sfm) is tool diameter 5 0.26 5 spindle speed (rpm). The formula for feed per tooth (fpt) is table feed (ipm)/number of flutes/spindle speed (rpm). The formula for spindle speed (rpm) is cutting speed (sfm) 5 3.82/tool diameter. The formula for table feed (ipm) is feed per tooth (ftp) 5 number of tool flutes 5 spindle speed (rpm).
- physical vapor deposition ( PVD)
physical vapor deposition ( PVD)
Tool-coating process performed at low temperature (500° C), compared to chemical vapor deposition (1,000° C). Employs electric field to generate necessary heat for depositing coating on a tool’s surface. See CVD, chemical vapor deposition.
- pitch
pitch
1. On a saw blade, the number of teeth per inch. 2. In threading, the number of threads per inch.
- threading
threading
Process of both external (e.g., thread milling) and internal (e.g., tapping, thread milling) cutting, turning and rolling of threads into particular material. Standardized specifications are available to determine the desired results of the threading process. Numerous thread-series designations are written for specific applications. Threading often is performed on a lathe. Specifications such as thread height are critical in determining the strength of the threads. The material used is taken into consideration in determining the expected results of any particular application for that threaded piece. In external threading, a calculated depth is required as well as a particular angle to the cut. To perform internal threading, the exact diameter to bore the hole is critical before threading. The threads are distinguished from one another by the amount of tolerance and/or allowance that is specified. See turning.