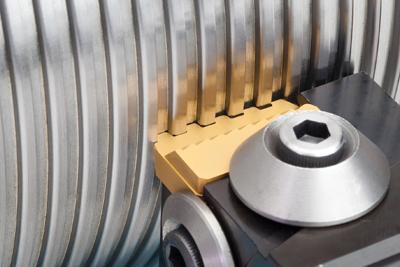
Seco developed its new thread chaser insert holder to bring high levels of precision and rigidity to threading operations that involve tough materials including the hard, gummy or high-chrome content ones used in the oil and gas industry. Such achievement is possible via a special carbide-pin locating system combined with a patented pocket seat surface pattern and high-pressure coolant capabilities.
Working in unison with top and axial clamps, the holder’s locating system uses two horizontally oriented pins that rest at specific distances from the bottom of the insert pocket. The exact points on the insert where these pins make contact are the same points that Seco works with when grinding the insert’s threading profile.
The two-pin system ensures extremely precise insert positioning from insert to insert as well as plays a key role in the holder’s increased rigidity and insert support. As a result, the holder helps reduce the number of threading passes required to produce a full thread profile.
The holder’s pocket seat surface pattern features milled scallops that provide even more chaser insert support. When the insert is mounted in the pocket, the clamping force acts on the scallop pattern and work hardens the seat surface to a hardness of 54 HRC.
Seco also equipped the holder with high-pressure coolant directed at key cutting areas of the insert. Coolant enters the holder from the back end, travels through the insert cavity directly to the insert’s chipformer and into the channels between each tooth. With a maximum output of 3,046 psi (210 bar), the holder delivers the industry’s highest coolant pressures for thread chasing operations.
The new thread chaser holder comes in two versions, P1 for 625" (15.875 mm) thick inserts and P5 for .984" (25 mm thick) inserts. Chipformer sizes come in .156" (3.97 mm) and .124" (3.18 mm).
Contact Details
Related Glossary Terms
- coolant
coolant
Fluid that reduces temperature buildup at the tool/workpiece interface during machining. Normally takes the form of a liquid such as soluble or chemical mixtures (semisynthetic, synthetic) but can be pressurized air or other gas. Because of water’s ability to absorb great quantities of heat, it is widely used as a coolant and vehicle for various cutting compounds, with the water-to-compound ratio varying with the machining task. See cutting fluid; semisynthetic cutting fluid; soluble-oil cutting fluid; synthetic cutting fluid.
- grinding
grinding
Machining operation in which material is removed from the workpiece by a powered abrasive wheel, stone, belt, paste, sheet, compound, slurry, etc. Takes various forms: surface grinding (creates flat and/or squared surfaces); cylindrical grinding (for external cylindrical and tapered shapes, fillets, undercuts, etc.); centerless grinding; chamfering; thread and form grinding; tool and cutter grinding; offhand grinding; lapping and polishing (grinding with extremely fine grits to create ultrasmooth surfaces); honing; and disc grinding.
- hardness
hardness
Hardness is a measure of the resistance of a material to surface indentation or abrasion. There is no absolute scale for hardness. In order to express hardness quantitatively, each type of test has its own scale, which defines hardness. Indentation hardness obtained through static methods is measured by Brinell, Rockwell, Vickers and Knoop tests. Hardness without indentation is measured by a dynamic method, known as the Scleroscope test.
- thread chaser
thread chaser
Die-type external threading tool. Makes final threading pass.
- threading
threading
Process of both external (e.g., thread milling) and internal (e.g., tapping, thread milling) cutting, turning and rolling of threads into particular material. Standardized specifications are available to determine the desired results of the threading process. Numerous thread-series designations are written for specific applications. Threading often is performed on a lathe. Specifications such as thread height are critical in determining the strength of the threads. The material used is taken into consideration in determining the expected results of any particular application for that threaded piece. In external threading, a calculated depth is required as well as a particular angle to the cut. To perform internal threading, the exact diameter to bore the hole is critical before threading. The threads are distinguished from one another by the amount of tolerance and/or allowance that is specified. See turning.