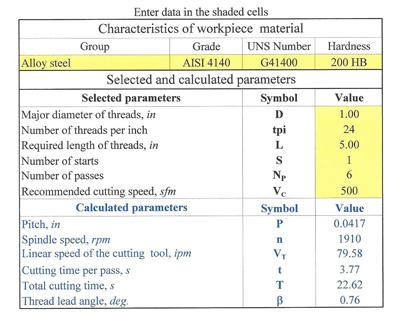
Threading is the process of creating a screw thread. More screw threads are produced each year than any other machine components.
The cutting tool moves across the workpiece linearly, taking chips off the workpiece with each pass. Number of passes depends on the number of threads per inch (tpi), workpiece material and its hardness.
Independent (selected) machining parameters for threading are: workpiece diameter, number of threads per inch, number of starts, and the cutting speed. Dependent (calculated) parameters are: pitch, spindle speed, linear speed of the cutting tool, thread lead angle, cutting time per pass, and total cutting time.
To be competitive, you have to create a screw thread at the maximum linear speed of the cutting tool (ipm). Since the linear speed of the cutting tool is directly proportional to the cutting speed (sfm), you have to know what the maximum cutting speed would be for a given workpiece material and its hardness. Information on the cutting speed data can be obtained from the cutting tool manufacturers.
Edmund Isakov, Ph.D., developed a threading calculator, which is functioning in Excel formulas. It includes major (computational) sheet and two sheets containing cutting speed data recommended by Sandvik Coromant.
It's not necessary to be "a rocket scientist" to use this calculator. Minimum system requirements: Windows 2000 or higher, Microsoft Excel 2000 or higher, CD-ROM Drive.
Contact Details
Related Glossary Terms
- cutting speed
cutting speed
Tangential velocity on the surface of the tool or workpiece at the cutting interface. The formula for cutting speed (sfm) is tool diameter 5 0.26 5 spindle speed (rpm). The formula for feed per tooth (fpt) is table feed (ipm)/number of flutes/spindle speed (rpm). The formula for spindle speed (rpm) is cutting speed (sfm) 5 3.82/tool diameter. The formula for table feed (ipm) is feed per tooth (ftp) 5 number of tool flutes 5 spindle speed (rpm).
- hardness
hardness
Hardness is a measure of the resistance of a material to surface indentation or abrasion. There is no absolute scale for hardness. In order to express hardness quantitatively, each type of test has its own scale, which defines hardness. Indentation hardness obtained through static methods is measured by Brinell, Rockwell, Vickers and Knoop tests. Hardness without indentation is measured by a dynamic method, known as the Scleroscope test.
- lead angle
lead angle
Angle between the side-cutting edge and the projected side of the tool shank or holder, which leads the cutting tool into the workpiece.
- pitch
pitch
1. On a saw blade, the number of teeth per inch. 2. In threading, the number of threads per inch.
- threading
threading
Process of both external (e.g., thread milling) and internal (e.g., tapping, thread milling) cutting, turning and rolling of threads into particular material. Standardized specifications are available to determine the desired results of the threading process. Numerous thread-series designations are written for specific applications. Threading often is performed on a lathe. Specifications such as thread height are critical in determining the strength of the threads. The material used is taken into consideration in determining the expected results of any particular application for that threaded piece. In external threading, a calculated depth is required as well as a particular angle to the cut. To perform internal threading, the exact diameter to bore the hole is critical before threading. The threads are distinguished from one another by the amount of tolerance and/or allowance that is specified. See turning.