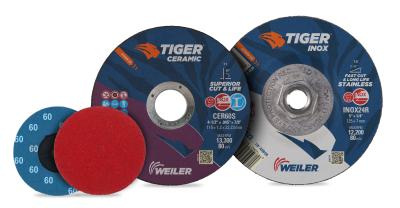
Weiler Abrasives, a global leader in abrasives and power brushes for surface conditioning, announced it will showcase the next evolution of abrasive solutions at FABTECH 2024, to be held Oct. 15 to 17 at the Orange County Convention Center in Orlando, Florida.
Changeovers cost time and money that operations don’t have to waste. Visitors to booth W3161 can find surface conditioning solutions to help them improve productivity and uptime, overcome labor challenges, and address safety issues. They can learn more about solutions for a variety of industries, including shipbuilding, metal fabrication, multipass welding and foundry applications.
Among the new solutions to be featured at the show will be the unique innovation in bonded formulation of the expanded Tiger 2.0 lineup, including the Tiger Ceramic 2.0 and Tiger INOX 2.0 portfolio of cutting, grinding and combination wheels. Tiger Ceramic 2.0 cutting, grinding and combo wheels offer a superior combination of life and cut rate for maximum productivity.
The unique design leverages innovative new ceramic grain technology that cuts extremely cool and removes material effortlessly while providing exceptional control for an improved operator experience. Extensive testing shows that the new ceramic wheels deliver an industry-leading 20% to 30% longer product life than the leading ceramic wheels on the market, with no reduction in cut rate. The INOX 2.0 wheels are designed for high performance when cutting and grinding high-value stainless steel parts. Premium aluminum oxide grains provide a smooth cut rate and consistent performance. Both Tiger Ceramic and Tiger INOX wheels are contaminant-free, so they are safe to use on stainless steel.
A new blending disc product lineup from Weiler Abrasives will also be featured in the booth. The blending discs, ideal for a wide range of blending, weld cleaning and polishing needs, can help operations save time and money through faster material removal and longer product life in such demanding industries as shipbuilding, structural fabrication and welding.
Weiler Abrasives specialists will also be scheduling consultations at the booth to help visitors understand their abrasive spend, along with ways to increase productivity and eliminate grinding and finishing bottlenecks. These essential consultations will include a thorough discussion of the steps needed to overcome surface conditioning challenges, whether related to labor, safety or increased customer demand. Specialists can also offer recommendations for better ways to grind and finish stainless steel, Inconel, aluminum and other hard-to-work-with materials — and how to choose the right abrasive for specific applications.
Contact Details
Related Glossary Terms
- abrasive
abrasive
Substance used for grinding, honing, lapping, superfinishing and polishing. Examples include garnet, emery, corundum, silicon carbide, cubic boron nitride and diamond in various grit sizes.
- aluminum oxide
aluminum oxide
Aluminum oxide, also known as corundum, is used in grinding wheels. The chemical formula is Al2O3. Aluminum oxide is the base for ceramics, which are used in cutting tools for high-speed machining with light chip removal. Aluminum oxide is widely used as coating material applied to carbide substrates by chemical vapor deposition. Coated carbide inserts with Al2O3 layers withstand high cutting speeds, as well as abrasive and crater wear.
- grinding
grinding
Machining operation in which material is removed from the workpiece by a powered abrasive wheel, stone, belt, paste, sheet, compound, slurry, etc. Takes various forms: surface grinding (creates flat and/or squared surfaces); cylindrical grinding (for external cylindrical and tapered shapes, fillets, undercuts, etc.); centerless grinding; chamfering; thread and form grinding; tool and cutter grinding; offhand grinding; lapping and polishing (grinding with extremely fine grits to create ultrasmooth surfaces); honing; and disc grinding.
- polishing
polishing
Abrasive process that improves surface finish and blends contours. Abrasive particles attached to a flexible backing abrade the workpiece.