Contact Details
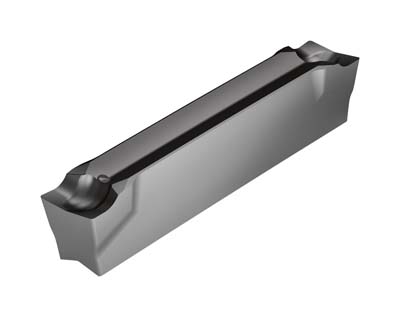
Walter USA LLC has unveiled the first indexable inserts with the new Tiger-tec Silver PVD aluminum oxide coating. These indexable grooving and cutoff inserts reportedly deliver superior tool life and increased productivity thanks to the advanced properties of the new coating. These properties include increased high-temperature wear resistance with no compromise in toughness.
The combination of toughness and wear resistance is a plus in any application, but particularly in grooving and cutoff operations because the tools experience several different conditions within the cut. For example, at the beginning of the cut the tools are exposed to a large amount of coolant, with little or none later. Similarly, there is high speed early in the cut with low speed later, and there is low stress on the tool early on, with high stress at the end of the cut.
Because of its optimized surface structure Tiger-tec Silver PVD lowers the friction on the cutting surface. Also, sharp and highly defined cutting edges can be achieved because the Tiger-tec Silver PVD coatings are thinner than conventional coatings. This fact, as well as the particularly smooth surface help to prevent build-up on the cutting edge and provide a high level of process reliability.
This advanced new coating will be made available in four grades: WSM13S, WSM23S, WSM33S and WSM43S. The cutting material WSM13S is suitable for use in stable machining conditions due to its distinctive hardness. The cutting material WSM43S is aimed at unstable clamping arrangements and machining conditions, low cutting speeds and interrupted cuts due to its excellent toughness properties. The middle variants WSM23S and WSM33S cover the relatively large intermediate range. This gives users an optimal grooving solution for each material and each application, with excellent tool life and process reliability.
Related Glossary Terms
- aluminum oxide
aluminum oxide
Aluminum oxide, also known as corundum, is used in grinding wheels. The chemical formula is Al2O3. Aluminum oxide is the base for ceramics, which are used in cutting tools for high-speed machining with light chip removal. Aluminum oxide is widely used as coating material applied to carbide substrates by chemical vapor deposition. Coated carbide inserts with Al2O3 layers withstand high cutting speeds, as well as abrasive and crater wear.
- coolant
coolant
Fluid that reduces temperature buildup at the tool/workpiece interface during machining. Normally takes the form of a liquid such as soluble or chemical mixtures (semisynthetic, synthetic) but can be pressurized air or other gas. Because of water’s ability to absorb great quantities of heat, it is widely used as a coolant and vehicle for various cutting compounds, with the water-to-compound ratio varying with the machining task. See cutting fluid; semisynthetic cutting fluid; soluble-oil cutting fluid; synthetic cutting fluid.
- cutoff
cutoff
Step that prepares a slug, blank or other workpiece for machining or other processing by separating it from the original stock. Performed on lathes, chucking machines, automatic screw machines and other turning machines. Also performed on milling machines, machining centers with slitting saws and sawing machines with cold (circular) saws, hacksaws, bandsaws or abrasive cutoff saws. See saw, sawing machine; turning.
- grooving
grooving
Machining grooves and shallow channels. Example: grooving ball-bearing raceways. Typically performed by tools that are capable of light cuts at high feed rates. Imparts high-quality finish.
- hardness
hardness
Hardness is a measure of the resistance of a material to surface indentation or abrasion. There is no absolute scale for hardness. In order to express hardness quantitatively, each type of test has its own scale, which defines hardness. Indentation hardness obtained through static methods is measured by Brinell, Rockwell, Vickers and Knoop tests. Hardness without indentation is measured by a dynamic method, known as the Scleroscope test.
- physical vapor deposition ( PVD)
physical vapor deposition ( PVD)
Tool-coating process performed at low temperature (500° C), compared to chemical vapor deposition (1,000° C). Employs electric field to generate necessary heat for depositing coating on a tool’s surface. See CVD, chemical vapor deposition.
- wear resistance
wear resistance
Ability of the tool to withstand stresses that cause it to wear during cutting; an attribute linked to alloy composition, base material, thermal conditions, type of tooling and operation and other variables.
Additional Products from Walter USA LLC
Pagination
- First page
- Previous page
- …
- 17
- 18
- 19
- 20
- 21
- 22
- 23
- 24
- 25