Contact Details
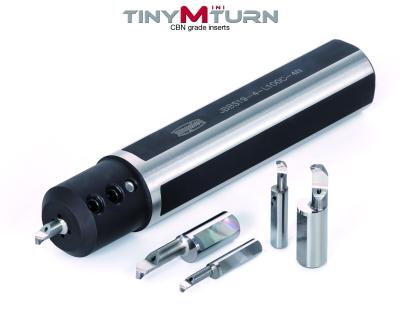
Tungaloy’s TinyMiniTurn mini boring bar tool line for small bore applications now offers CBN tipped boring bars for machining hardened steel parts.
TinyMiniTurn offers a wide range of geometry types and grades that provide excellent performance in small diameter boring applications. The line boasts a full range of solid carbide mini boring bars that allows machining from as small as 0.6 millimeter (.024 inch) diameters, as well as indexable boring tools that use a tiny insert in the inscribed circle of 3.57 millimeters (9/64 inches) or 3.97 millimeters (5/32 inches).
New CBN-tipped mini boring bars feature BX310 uncoated CBN grade that increases the grade’s wear resistance when used at low to medium cutting speeds, making it perfect for machining small bores from as small as 2.8 millimeter (.110 inch) diameter of hardened steel parts.
The JBT-style cutting edge geometry of the new bars incorporates a 98 degree point angle that allows the single geometry to be used in multiple applications, including boring, profiling, and chamfering. Furthermore, the boring bars feature an edge preparation of 0.13 mm (.005″) x 15° chamfer, providing the cutting edge with edge-line security and robustness.
The new CBN boring bars are equipped with internal coolant channel for through-coolant capability. This feature allows the coolant jet to be directed exactly to the optimal position accurately to cutting point for increased tool life and chip control, which was difficult with conventional external coolant supply method, during small diameter boring operations.
Related Glossary Terms
- boring
boring
Enlarging a hole that already has been drilled or cored. Generally, it is an operation of truing the previously drilled hole with a single-point, lathe-type tool. Boring is essentially internal turning, in that usually a single-point cutting tool forms the internal shape. Some tools are available with two cutting edges to balance cutting forces.
- boring bar
boring bar
Essentially a cantilever beam that holds one or more cutting tools in position during a boring operation. Can be held stationary and moved axially while the workpiece revolves around it, or revolved and moved axially while the workpiece is held stationary, or a combination of these actions. Installed on milling, drilling and boring machines, as well as lathes and machining centers.
- chamfering
chamfering
Machining a bevel on a workpiece or tool; improves a tool’s entrance into the cut.
- coolant
coolant
Fluid that reduces temperature buildup at the tool/workpiece interface during machining. Normally takes the form of a liquid such as soluble or chemical mixtures (semisynthetic, synthetic) but can be pressurized air or other gas. Because of water’s ability to absorb great quantities of heat, it is widely used as a coolant and vehicle for various cutting compounds, with the water-to-compound ratio varying with the machining task. See cutting fluid; semisynthetic cutting fluid; soluble-oil cutting fluid; synthetic cutting fluid.
- cubic boron nitride ( CBN)
cubic boron nitride ( CBN)
Crystal manufactured from boron nitride under high pressure and temperature. Used to cut hard-to-machine ferrous and nickel-base materials up to 70 HRC. Second hardest material after diamond. See superabrasive tools.
- edge preparation
edge preparation
Conditioning of the cutting edge, such as a honing or chamfering, to make it stronger and less susceptible to chipping. A chamfer is a bevel on the tool’s cutting edge; the angle is measured from the cutting face downward and generally varies from 25° to 45°. Honing is the process of rounding or blunting the cutting edge with abrasives, either manually or mechanically.
- inscribed circle ( IC)
inscribed circle ( IC)
Imaginary circle that touches all sides of an insert. Used to establish size. Measurements are in fractions of an inch and describe the diameter of the circle.
- point angle
point angle
Included angle at the point of a twist drill or similar tool; for general-purpose tools, the point angle is typically 118°.
- profiling
profiling
Machining vertical edges of workpieces having irregular contours; normally performed with an endmill in a vertical spindle on a milling machine or with a profiler, following a pattern. See mill, milling machine.
- wear resistance
wear resistance
Ability of the tool to withstand stresses that cause it to wear during cutting; an attribute linked to alloy composition, base material, thermal conditions, type of tooling and operation and other variables.