Contact Details
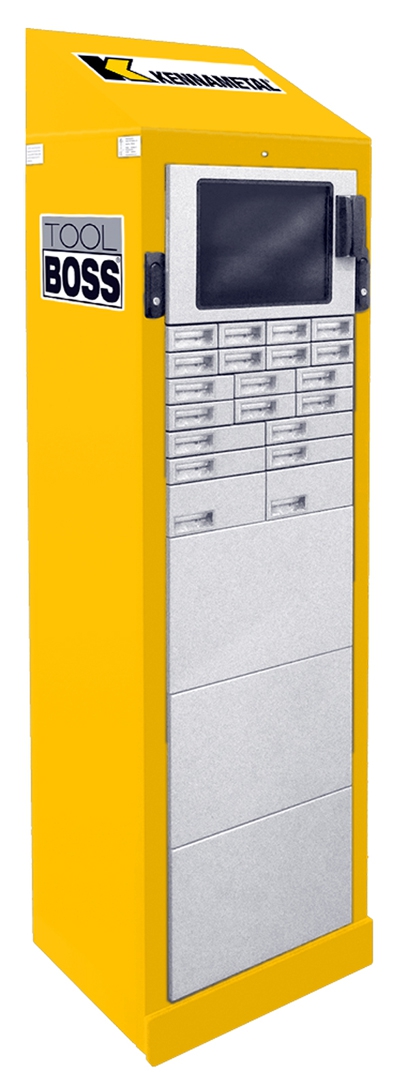
One of the most fundamental keys to running an efficient and cost-effective plant is having the right tool in the right place at the right time. While the cost of a milling or turning insert may range from a few dollars to significant investment, not having that tool available when needed can shut down an entire production line or more, resulting in missed delivery dates and lost profits. That is why tooling technology leader Kennametal Inc. is announcing new expansions of its ToolBOSS tool-management system.
"More and more customers are demanding vending solutions for all the classic reasons," says Jay Evans, Kennametal program manager for global supply chain services. "They all want to improve inventory control, downsize centralized tool crib operations, reduce the amount of time it takes for machine operators to locate required tools, and capture, compare, and trend tooling costs associated with the part produced. Such data helps identify problem areas and opportunities for continuous-improvement efforts."
The newest ToolBOSS model is a smaller, portable demo unit that Kennametal is making available to its distribution channel partners. "Distributors are the front line in customizing programs for their customers," Evans says. "The demo unit is a great way for those distributors to demonstrate ToolBOSS advantages right in their own conference rooms.
At only 100lbs (45 kg), the demo unit includes a ToolBOSS computer loaded with the full version of ToolBOSS Inventory Manager software, the standard touch screen, and two pre-configured tray levels. "Width- and depth-wise, the demo unit is a full-size ToolBOSS frame, but the height is only 23 inches (58.4 cm)," Evans says. "This allows our distributor partners to show a variety of tray and drawer sizes — solutions for large and small shops alike."
The Flex Unit is a full-size ToolBOSS frame that starts out with eight drawers to further showcase ToolBOSS advantages. As customer requirements grow, more drawers can be added up to 26 levels to the frame "Trays and drawers can be configured not only for tooling, but also other shop needs such as belts, wheels, gloves, and other equipment," says Evans.
Appropriate to its name, the ToolBOSS Modulo unit is a modular ToolBOSS frame that can be configured to provide different drawer and compartment sizes, expanding ToolBOSS for more than just tools, but also anything else companies want to more efficiently control, such as replacement parts, gloves and personal items.
Related Glossary Terms
- gang cutting ( milling)
gang cutting ( milling)
Machining with several cutters mounted on a single arbor, generally for simultaneous cutting.
- milling
milling
Machining operation in which metal or other material is removed by applying power to a rotating cutter. In vertical milling, the cutting tool is mounted vertically on the spindle. In horizontal milling, the cutting tool is mounted horizontally, either directly on the spindle or on an arbor. Horizontal milling is further broken down into conventional milling, where the cutter rotates opposite the direction of feed, or “up” into the workpiece; and climb milling, where the cutter rotates in the direction of feed, or “down” into the workpiece. Milling operations include plane or surface milling, endmilling, facemilling, angle milling, form milling and profiling.
- turning
turning
Workpiece is held in a chuck, mounted on a face plate or secured between centers and rotated while a cutting tool, normally a single-point tool, is fed into it along its periphery or across its end or face. Takes the form of straight turning (cutting along the periphery of the workpiece); taper turning (creating a taper); step turning (turning different-size diameters on the same work); chamfering (beveling an edge or shoulder); facing (cutting on an end); turning threads (usually external but can be internal); roughing (high-volume metal removal); and finishing (final light cuts). Performed on lathes, turning centers, chucking machines, automatic screw machines and similar machines.