Contact Details
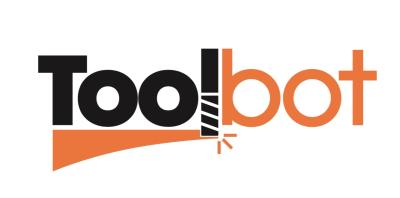
IMCO Carbide Tool Inc. is rolling out an advanced customer “ToolBot” that makes generating carbide end mill feeds and speeds faster and more accurate, because results are customized for the user’s machining task and machine limits, the company announced today.
“‘ToolBot’ uses prompts and simple dropdown menus that make it incredibly versatile, fast and user friendly,” explained Matt Osburn, VP, Technical Director. “But don’t let the simplicity fool you. This program is powered by the latest in high-speed database technology to help our customers stay a step ahead.”
The intuitive nature of ToolBot allows programmers and machinists alike to enter four simple pieces of information – end mill, material, cut type and machine limits – into the online program, and ToolBot does the rest, explained Osburn. Prompts and dropdowns make entries fast and easy.
Users can select from up to nine common milling cut types from a dropdown menu. ToolBot automatically filters out cut types that are not recommended for the end mill/material combination, thereby avoiding poor machining results. In addition, ToolBot automatically adjusts cutting parameters based on the user’s machine.
Steve Avers, IMCO’s Technical Support Manager, said final ToolBot recommendations will incorporate tool projection from the spindle in the speed and feed data, as well as provide ramp angles, machine horsepower and rpm required, and cut dimensions and layers needed. Users also can customize the recommendations to suit their needs, all without doing any mathematical calculations.
“Fast, easy and customizable cutting parameters are now available 24/7 for all of our customers, programmers and machinists,” Avers explained. “It really couldn’t be easier.”
Basic ToolBot features are available to all, Osburn said, but advanced features, such as saving and sharing ToolBot results, are available only to users who set up a free ToolBot registration. Registered users can archive and share cutting parameters within their organization, so having an account and login really pays off.
“As with all IMCO advanced technology, ToolBot helps give our customers the edge in a competitive industry to achieve higher productivity and profitability,” Osburn said. “That’s what we do best.”
Related Glossary Terms
- feed
feed
Rate of change of position of the tool as a whole, relative to the workpiece while cutting.
- gang cutting ( milling)
gang cutting ( milling)
Machining with several cutters mounted on a single arbor, generally for simultaneous cutting.
- milling
milling
Machining operation in which metal or other material is removed by applying power to a rotating cutter. In vertical milling, the cutting tool is mounted vertically on the spindle. In horizontal milling, the cutting tool is mounted horizontally, either directly on the spindle or on an arbor. Horizontal milling is further broken down into conventional milling, where the cutter rotates opposite the direction of feed, or “up” into the workpiece; and climb milling, where the cutter rotates in the direction of feed, or “down” into the workpiece. Milling operations include plane or surface milling, endmilling, facemilling, angle milling, form milling and profiling.
- milling machine ( mill)
milling machine ( mill)
Runs endmills and arbor-mounted milling cutters. Features include a head with a spindle that drives the cutters; a column, knee and table that provide motion in the three Cartesian axes; and a base that supports the components and houses the cutting-fluid pump and reservoir. The work is mounted on the table and fed into the rotating cutter or endmill to accomplish the milling steps; vertical milling machines also feed endmills into the work by means of a spindle-mounted quill. Models range from small manual machines to big bed-type and duplex mills. All take one of three basic forms: vertical, horizontal or convertible horizontal/vertical. Vertical machines may be knee-type (the table is mounted on a knee that can be elevated) or bed-type (the table is securely supported and only moves horizontally). In general, horizontal machines are bigger and more powerful, while vertical machines are lighter but more versatile and easier to set up and operate.