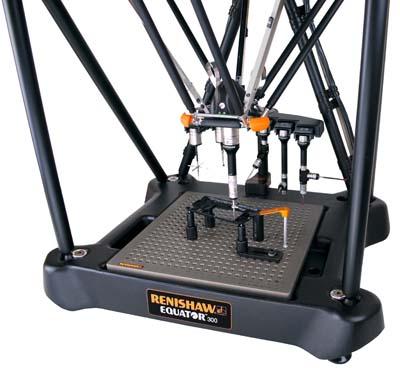
Renishaw's Equator shop-floor comparative gauge gets a significant speed boost for single-point probing applications with new touch-trigger probing capability via the TP20 probe, which can now be used in addition to the scanning SP25 probe. The two probing technologies allow the choice of the fastest data capture technique for each application or part.
Equator with TP20 is an ideal alternative for in-line gauging tasks which might have used expensive custom hard gauges with single-point air gauges or LVDTs. TP20 can be used for fast capture of discrete point data, with the stiff lightweight structure of Equator allowing very short cycle times and high repeatability on simple touch point measurements. The touch trigger kit includes robust industry-standard TP20 modules and a new range of extension bars and joints. The Equator can also switch automatically to the SP25 scanning module using the integrated changing rack to provide any combination of measurement routines. SP25 allows continuous scanning of features at scan speeds of up to 200mm/s, to gather high volumes of data on the form of features.
Equator uses the principle of mastering to cope with changes in temperature on the shop floor, and the process of calibrating the master part is now faster with the new Feature Compare function. Master parts do not need to be expensive or custom made; users can simply take a production part and measure it in any number of ways, such as on a calibrated coordinate measuring machine in a temperature-controlled environment. This measurement establishes the variation of the master part from the CAD or drawing nominals. Feature Compare then allows the user to simply take the master part's measurement data and enter the compensation values for each feature's size, position or orientation relative to the CAD or drawing nominals. The simple and unique Feature Compare interface has been designed for effortless data input.
Remastering Equator on the shop floor with the master part is as fast as measuring a production part and immediately compensates for any change in the thermal conditions of a shop-floor environment. Equator can be used in factories with wide temperature variation. Simply remaster and the system is "rezeroed" and ready for repeatable comparison measurements.
The calibrated absolute accuracy of the CMM or other devices (often kept in a temperature-controlled metrology lab) can be effectively "extended" onto the shop floor to provide calibrated traceability to Equator measurements. With the calibration data for the master part loaded into the Equator software, measurements then made on the Equator gauge can be referred back to the CAD or drawing nominals for traceability to a calibrated device.
Equator inspection programs can be created or modified with Renishaw's comprehensive MODUS programming software. Shop-floor operators then simply select and run the programs using the intuitive Organiser front-end software. Organiser software can report gauging results as a simple pass/fail message, as a full inspection report, or through the Process Monitor window.
Contact Details
Related Glossary Terms
- calibration
calibration
Checking measuring instruments and devices against a master set to ensure that, over time, they have remained dimensionally stable and nominally accurate.
- computer-aided design ( CAD)
computer-aided design ( CAD)
Product-design functions performed with the help of computers and special software.
- metrology
metrology
Science of measurement; the principles on which precision machining, quality control and inspection are based. See precision machining, measurement.