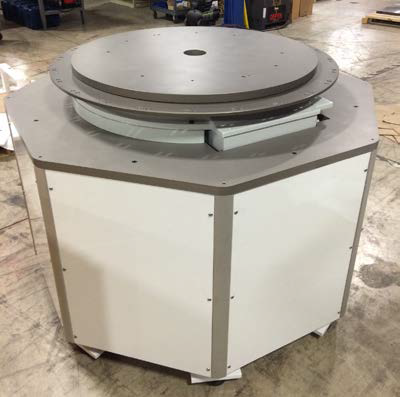
WEISS and its subsidiary WEISS North America Inc. recently completed three, turnkey TR1100, ring-style chassis systems for a leading West Coast medical parts manufacturer. Their client‘s diverse medical product line provides patients and caregivers safe, innovative, life-enhancing medical devices that help improve patient outcomes by minimizing bacterial ingress that can cause bloodstream infections, and preventing exposure to infectious diseases or hazardous drugs. The most recent manufacturing challenge was for a closed female luer valve, that would require a robust system featuring 24 install stations for a 3- to 5-piece assembly production process.
Whereas the medical parts client had only a small build shop, they sought out WEISS to provide a one-stop solution that would allow them to maximize efficiencies, while granting them more time to focus on multiple projects. They also desired a quiet, smooth running system for their clean room application. The key to the WEISS solution involved the TR1100 ring-style chassis featuring a ring indexer, stationary plates, and riser. These were all housed in a unique octagon-shaped frame design, that is enclosed with a guarding system on the lower half for protective access to controls and mounting automation.
The comprehenisve system was manufactured, tooled, mounted, and machined complete by WEISS at its Willoughby, Ohio, facility, and delivered to the client as a one-source, preassembled medical parts assembly solution. WEISS engineers faced the task of building a base machine chassis that can accommodate 24 install stations for a 3- to 5-piece multiple size medical valve assembly process that included: loading, pressing, ultrasonic welding, leak testing, inspection and ejecting.
Ultimately, this proved no problem for WEISS as the combination of robust construction of the TR1100 series system and octagon frame design provided more than enough scope for coupling with the multiple processing stations.
At the heart of the system, the TR1100 series rotary indexing rings feature a large central opening (up to 1,750 mm possible), extremely flat design and a high level of parts accuracy. The ring-shaped design allows extra free design space, and the rotating aluminium ring can be adjusted to client‘s specifications in terms of diameter and thickness.
WEISS’s TR1100 modified chassis design was based on the client‘s request for the octagon shaped frame beneath the top plate. This fully enclosed guarding undercarriage system is comprised of a combination of aluminum extrusion and sheet metal fabrications that included six bolt-on panels and two swinging door panels for access to controls. The entire frame was powder coated.
The frame extrusion also needed to be flush with both the top plate and the mount enclosure doors. The index table has a 2“-thick aluminum riser, the octagon table top is 63” across flats and 1.25” thick. The 48”-dia. aluminium dial plate is 1.00” thick and the 44”-dia. stationary tool plate is 1.25” thick. All chassis system plates featured a hard coat anodized finish that is essential in providing superior durability.
Contact Details
Related Glossary Terms
- extrusion
extrusion
Conversion of an ingot or billet into lengths of uniform cross section by forcing metal to flow plastically through a die orifice.
- flat ( screw flat)
flat ( screw flat)
Flat surface machined into the shank of a cutting tool for enhanced holding of the tool.
- lapping compound( powder)
lapping compound( powder)
Light, abrasive material used for finishing a surface.