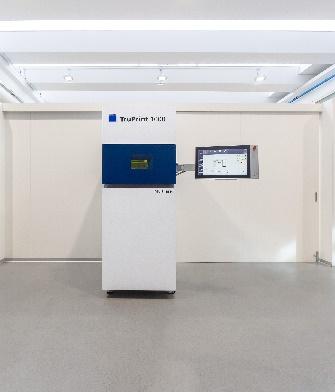
TRUMPF is introducing the new TruPrint 1000 for additive series production to the North American market. The productive and compact entry-level system for 3D additive processing of metal powders was redesigned for the manufacture of dental prostheses or medical technology but is also impressive in R&D or small series production.
“The new TruPrint machine is two times faster than its predecessor and is ideally suited for series production, especially in the dental or medical technology industry," says Adam Simons, head of additive manufacturing sales & product at TRUMPF Inc. “It is one of the best choices on the market for processing titanium thanks to the machine’s inert powder cycle and very low gas consumption.”
Improved series production
The printer features two 200-watt lasers and a multiplate option, which allow users to run multiple builds without operator intervention by automatically exchanging the build plate. Users can stack up to four build plates on top of each other in the build cylinder, and the system prints components on them one after the other. "The TruPrint 1000 can produce overnight or on weekends, running multiple jobs automatically without a worker having to be present,” Simons explains. “Users save a lot of time and costs too.”
A new compact design means the TruPrint 1000 only uses half of the floor space needed by previous editions and can pass easily through a standard door. Even in smaller production environments, users can have several machines producing side by side in parallel to further speed up series production.
The TruPrint 1000 can easily produce dental prostheses, i.e., crowns, bridges and cast models, from cobalt-chrome or titanium alloys. “The machine was redesigned to meet the specific needs of the dental market,” adds Simons. “Using the Multilaser with a preform, up to 64 individual abutments can be printed in approximately one hour.” The system is also suitable for medical technology manufacturers or prototype construction in many other industries.
Exchange cylinder principle speeds up production
With an exchange kit, the build, powder and overflow cylinders of the TruPrint 1000 are quick and easy to change. Filters are easily accessible on the side of the machine and users can change them quickly. A material change, such as from cobalt-chrome to titanium, can be completed in just 15 to 20 minutes. Brushes and gloves are integrated into the machine. The user can clean the additively manufactured components and unpack the build job - without opening the door. "This is a big advantage," says Simons. “If powder swirls up, machine operators can't contaminate themselves with the material.”
Improved gas flow makes system fast and reliable
TRUMPF improved the flow of the shielding gas during the production process. "Thanks to the primary and secondary flow, the work area remains clean even after several build jobs and the protective glass does not become contaminated,” says Simons. “The same is true when processing tool steel, which can be prone to heavy fuming.” If the protective glass does get dirty, the machine operator can remove and clean it in a few easy steps. The sophisticated gas flow also ensures a consistent production process, as predefined laser power always reaches the powder. Thanks to the clean working environment, users can apply higher layer thicknesses. This increases the productivity of the system and improves the quality of the additively manufactured components.
TruPrint 1000 can print with two lasers
The TruPrint 1000 works particularly quickly and reliably. In the Multilaser version, the system has two lasers and both lasers can process the entire build plate. "With two lasers we can improve the productivity of this machine even further," says Simons. The TruPrint 1000 also uses a beam expander to automatically adjust the spot diameter of the laser for the particular build job. The spot diameter is 55 or 80 micrometers, depending on the application. The wider spot allows for higher productivity, while the 55-micrometer spot can be used when special powders need higher energy density.
Contact Details
Related Glossary Terms
- alloys
alloys
Substances having metallic properties and being composed of two or more chemical elements of which at least one is a metal.
- lapping compound( powder)
lapping compound( powder)
Light, abrasive material used for finishing a surface.
- parallel
parallel
Strip or block of precision-ground stock used to elevate a workpiece, while keeping it parallel to the worktable, to prevent cutter/table contact.