Contact Details
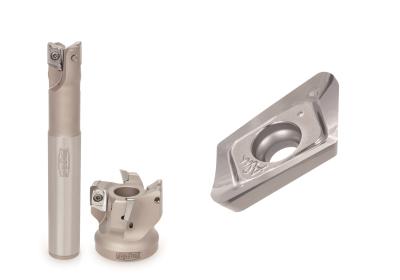
Tungaloy has expanded its Tung-AluMill line of indexable shoulder milling cutters to include an insert with a 2.5 mm (0.1") nose radii.
The Tung-AluMill line of indexable square shoulder milling cutters features V bottom inserts and secure insert retention, enabling high-speed milling of aluminum alloys and other nonferrous materials. This cutter ensures stability and efficiency in shouldering, slotting and profiling applications at elevated cutting speeds.
The use of lightweight, high-strength aluminum alloys is increasing across many industries to reduce environmental burdens. More specifically, the aerospace industry is using aluminum alloys for large aircraft components to meet weight reduction requirements for improved fuel efficiency. Tung-AluMill’s new 2.5 mm nose radius insert enhances its comprehensive lineup of insert radii preferred by aircraft component manufacturers to boost productivity and cost effectiveness.
At a glance:
Process security at high revolutions: insert bottom ensures centrifugal protection and secure milling process
High efficiency: cutting edge toughness and fracture resistance enable milling at higher feeds and speeds
One insert to be added: XVCT160525R-AJ TH10
Related Glossary Terms
- alloys
alloys
Substances having metallic properties and being composed of two or more chemical elements of which at least one is a metal.
- aluminum alloys
aluminum alloys
Aluminum containing specified quantities of alloying elements added to obtain the necessary mechanical and physical properties. Aluminum alloys are divided into two categories: wrought compositions and casting compositions. Some compositions may contain up to 10 alloying elements, but only one or two are the main alloying elements, such as copper, manganese, silicon, magnesium, zinc or tin.
- gang cutting ( milling)
gang cutting ( milling)
Machining with several cutters mounted on a single arbor, generally for simultaneous cutting.
- milling
milling
Machining operation in which metal or other material is removed by applying power to a rotating cutter. In vertical milling, the cutting tool is mounted vertically on the spindle. In horizontal milling, the cutting tool is mounted horizontally, either directly on the spindle or on an arbor. Horizontal milling is further broken down into conventional milling, where the cutter rotates opposite the direction of feed, or “up” into the workpiece; and climb milling, where the cutter rotates in the direction of feed, or “down” into the workpiece. Milling operations include plane or surface milling, endmilling, facemilling, angle milling, form milling and profiling.
- profiling
profiling
Machining vertical edges of workpieces having irregular contours; normally performed with an endmill in a vertical spindle on a milling machine or with a profiler, following a pattern. See mill, milling machine.
- slotting
slotting
Machining, normally milling, that creates slots, grooves and similar recesses in workpieces, including T-slots and dovetails.