Contact Details
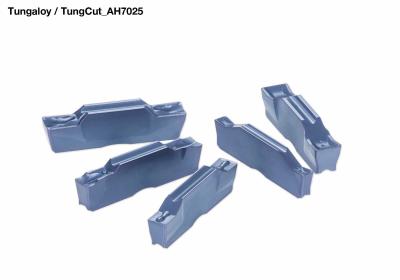
Tungaloy offers AH7025, the versatile PVD grade for TungCut, the multifunctional grooving tool with 2-cornered inserts. TungCut provides stable and long tool life because of its unique rigid insert clamping system, according to the company. The tool series covers a wide variety of grooving operations from small-part machining to general machining.
AH7025 is a new versatile PVD grade that realizes high level of wear and chipping resistance due to the combination of the new coating layer and the substrate, which makes the grade ideal for all grooving needs.
AH7025 is applicable for a variety of materials, including steel, stainless steel and even heat-resistant alloys and suitable for all types of applications, such as grooving, turning and parting.
Related Glossary Terms
- alloys
alloys
Substances having metallic properties and being composed of two or more chemical elements of which at least one is a metal.
- grooving
grooving
Machining grooves and shallow channels. Example: grooving ball-bearing raceways. Typically performed by tools that are capable of light cuts at high feed rates. Imparts high-quality finish.
- parting
parting
When used in lathe or screw-machine operations, this process separates a completed part from chuck-held or collet-fed stock by means of a very narrow, flat-end cutting, or parting, tool.
- physical vapor deposition ( PVD)
physical vapor deposition ( PVD)
Tool-coating process performed at low temperature (500° C), compared to chemical vapor deposition (1,000° C). Employs electric field to generate necessary heat for depositing coating on a tool’s surface. See CVD, chemical vapor deposition.
- turning
turning
Workpiece is held in a chuck, mounted on a face plate or secured between centers and rotated while a cutting tool, normally a single-point tool, is fed into it along its periphery or across its end or face. Takes the form of straight turning (cutting along the periphery of the workpiece); taper turning (creating a taper); step turning (turning different-size diameters on the same work); chamfering (beveling an edge or shoulder); facing (cutting on an end); turning threads (usually external but can be internal); roughing (high-volume metal removal); and finishing (final light cuts). Performed on lathes, turning centers, chucking machines, automatic screw machines and similar machines.