Contact Details
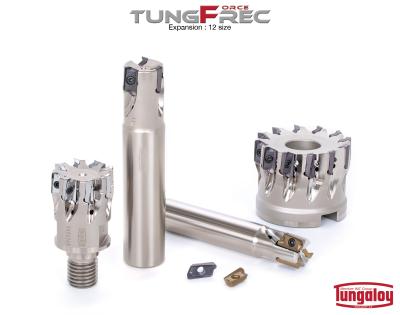
Tungaloy has announced an expansion of TungForce-Rec square shoulder milling cutter series by including size 12 inserts and associated cutter bodies.
TungForce-Rec is a high-density shoulder milling cutter series with a secure insert clamping system that boasts excellent process security. Carrying all the advantages of the existing size 06 V-bottom inserts, the new size 12 inserts offer an extended cutting edge length that is twice as long as the size 06. The cutter body also features the same rigid design as TungForce-Rec 06, being furnished with a thick core diameter and heavily supported backing behind the insert. These features enable the use of longer insert clamping screws for greater screw-thread engagement security, ensuring tool reliability when used at a high metal removal rate.
TungForce-Rec 12 boasts 1.5 times higher tooth density than other competing shoulder milling cutters of the same size, allowing a 16 mm (5/8″) diameter cutter to carry 3 teeth and 50 mm (2″) 12 teeth. As such, the new shoulder milling cutter can run at a higher table feed than competitors when being fed at the same rate per tooth.
The new TungForce-Rec 12 offers cutter bodies available in cylindrical shanks either with standard length shanks or long shanks, modular heads with a self-centering screw coupling, and shell mills. 26 total inserts have been introduced, in geometries including MM style for general purpose with nose radii ranging from 0.4 to 3.0 mm (from .016″ to .118″) and AM style for aluminum alloy with nose radii of 0.4 and 0.8 mm (.016″ and .031″).
Related Glossary Terms
- backing
backing
1. Flexible portion of a bandsaw blade. 2. Support material behind the cutting edge of a tool. 3. Base material for coated abrasives.
- feed
feed
Rate of change of position of the tool as a whole, relative to the workpiece while cutting.
- gang cutting ( milling)
gang cutting ( milling)
Machining with several cutters mounted on a single arbor, generally for simultaneous cutting.
- milling
milling
Machining operation in which metal or other material is removed by applying power to a rotating cutter. In vertical milling, the cutting tool is mounted vertically on the spindle. In horizontal milling, the cutting tool is mounted horizontally, either directly on the spindle or on an arbor. Horizontal milling is further broken down into conventional milling, where the cutter rotates opposite the direction of feed, or “up” into the workpiece; and climb milling, where the cutter rotates in the direction of feed, or “down” into the workpiece. Milling operations include plane or surface milling, endmilling, facemilling, angle milling, form milling and profiling.
- milling cutter
milling cutter
Loosely, any milling tool. Horizontal cutters take the form of plain milling cutters, plain spiral-tooth cutters, helical cutters, side-milling cutters, staggered-tooth side-milling cutters, facemilling cutters, angular cutters, double-angle cutters, convex and concave form-milling cutters, straddle-sprocket cutters, spur-gear cutters, corner-rounding cutters and slitting saws. Vertical cutters use shank-mounted cutting tools, including endmills, T-slot cutters, Woodruff keyseat cutters and dovetail cutters; these may also be used on horizontal mills. See milling.