Contact Details
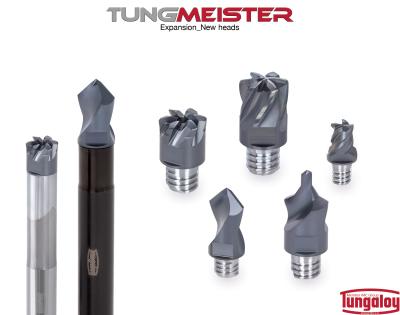
Tungaloy has added 88 total exchangeable heads in five geometries to its TungMeister exchangeable milling head range: VFX high feed milling heads, VBL lens-shape milling head for 5-axis machining, VEE small-diameter square shoulder milling head, VDS spot drilling and chamfering head, and VDP center drilling head.
VFX milling head for high feed applications now offers 6 flute version, in addition to existing 2- and 4-fluted milling heads, enabling TungMeister for higher productivity machining. The new 6-flute milling head is available in AH750 grade suitable for high productivity machining of ISO H materials. Additionally, existing 2- and 4-fluted milling heads are offered with through-coolant channels as well, which direct precision coolant supply close to the cutting point for improved tool life and chip evacuation.
In addition to standard VBO and VBN barrel-shaped end mills for productive finish machining of curved surfaces, TungMeister’s new VBL lens-shape milling head has a convexly shaped cutting edge on the tool’s tip, instead of on the periphery, providing a good solution for machining a complex bottom surface. These end milling heads enable more material removal with fewer passes in 5-axis machining.
VEE square shoulder end milling heads are now available with a S04-size screw thread for secure and accurate coupling of a 6 mm diameter VEE head with the shanks in the same diameter of 6 mm. This feature makes it easier to use TungMeister VEE in Swiss machining applications.
VDS is a spot drilling head for creating a small dent on the surface of the material to correctly locate the center of a drill when commencing a penetration, eliminating the risk of drill walking and helping to ensure more accurate hole dimensions. The spot drill tip and helical flute designs are optimized for smooth material engagement. Since the tip angle of the VDS head is 90 degrees, it can also be used for 45 degree chamfering process.
The VDP center drill head now includes Type B, forming a hole with two chamfers: a 60 degree chamfer and 120 degree chamfer at the start of the hole in a single drilling operation.
The TungMeister series
TungMeister is designed to minimize machine downtime, requiring no more than one minute for tool exchange. Setup time can significantly be reduced to as short as one tenth of the time it would typically take to replace solid carbide end mills for maximum productivity and cost effectiveness. With over 13,000 possible head-shank combinations available, TungMeister provides tooling flexibility that enables users to find a solution for almost every milling application.
Related Glossary Terms
- center drill
center drill
Drill used to make mounting holes for workpiece to be held between centers. Also used to predrill holes for subsequent drilling operations. See centers.
- center drilling
center drilling
Drilling tapered holes for mounting workpiece between centers. Center-drilled holes also serve as starter holes for drilling larger holes in the same location. See centers; drilling.
- chamfering
chamfering
Machining a bevel on a workpiece or tool; improves a tool’s entrance into the cut.
- coolant
coolant
Fluid that reduces temperature buildup at the tool/workpiece interface during machining. Normally takes the form of a liquid such as soluble or chemical mixtures (semisynthetic, synthetic) but can be pressurized air or other gas. Because of water’s ability to absorb great quantities of heat, it is widely used as a coolant and vehicle for various cutting compounds, with the water-to-compound ratio varying with the machining task. See cutting fluid; semisynthetic cutting fluid; soluble-oil cutting fluid; synthetic cutting fluid.
- feed
feed
Rate of change of position of the tool as a whole, relative to the workpiece while cutting.
- gang cutting ( milling)
gang cutting ( milling)
Machining with several cutters mounted on a single arbor, generally for simultaneous cutting.
- milling
milling
Machining operation in which metal or other material is removed by applying power to a rotating cutter. In vertical milling, the cutting tool is mounted vertically on the spindle. In horizontal milling, the cutting tool is mounted horizontally, either directly on the spindle or on an arbor. Horizontal milling is further broken down into conventional milling, where the cutter rotates opposite the direction of feed, or “up” into the workpiece; and climb milling, where the cutter rotates in the direction of feed, or “down” into the workpiece. Milling operations include plane or surface milling, endmilling, facemilling, angle milling, form milling and profiling.