Contact Details
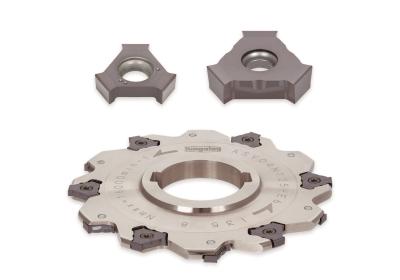
Tungaloy expands its TungThinSlit line of indexable slot milling cutters to include inserts that feature F (sharp) cutting edge preparation. The TungThinSlit slot milling cutter consists of indexable inserts with a unique structure.
The double-sided insert can be used for either the right- or left-hand cutting edge reversibly. Economical, the six cutting-edge insert reduces tool costs and inventory management.
TungThinSlit is capable of milling narrow slots of widths ranging from 4 to 8 mm (from 0.157" to 0.315"), which are often seen on automotive parts, such as steering knuckles and shafts. These components usually lack rigidity or are often fixed in weak setups constraining the application from improving the feed per tooth (fz). In addition, in the slim slot milling range that TungThinSlit is capable of, the ratio of the radial engagement of the cutter in relation to the cutter diameter, or ae/Dc tends to be less than 15%, producing extremely thin chips of less than 0.02 mm (0.00079") chip thickness.
Manufacturers usually go to carbide brazed slot cutters with sharp positive cutting edges to reduce cutting forces and improve chip flow for machining stability because conventional slot milling inserts with honed cutting edges create vibrations and burrs on the workpiece. The new F-edged TungThinSlit inserts reduce the cutting forces eliminating vibrations and burr formations, while maximizing surface finish and productivity.
At a glance:
F (sharp) cutting edge preparation for free-cutting action
SH725-grade coating maintains cutting edge sharpness and strength
Reduces chatter and burr formation
Economical, six-edged inserts for easy tool management. A single insert shape for the right- and left-hand cutting
Total of four inserts to be introduced
Related Glossary Terms
- burr
burr
Stringy portions of material formed on workpiece edges during machining. Often sharp. Can be removed with hand files, abrasive wheels or belts, wire wheels, abrasive-fiber brushes, waterjet equipment or other methods.
- chatter
chatter
Condition of vibration involving the machine, workpiece and cutting tool. Once this condition arises, it is often self-sustaining until the problem is corrected. Chatter can be identified when lines or grooves appear at regular intervals in the workpiece. These lines or grooves are caused by the teeth of the cutter as they vibrate in and out of the workpiece and their spacing depends on the frequency of vibration.
- edge preparation
edge preparation
Conditioning of the cutting edge, such as a honing or chamfering, to make it stronger and less susceptible to chipping. A chamfer is a bevel on the tool’s cutting edge; the angle is measured from the cutting face downward and generally varies from 25° to 45°. Honing is the process of rounding or blunting the cutting edge with abrasives, either manually or mechanically.
- feed
feed
Rate of change of position of the tool as a whole, relative to the workpiece while cutting.
- gang cutting ( milling)
gang cutting ( milling)
Machining with several cutters mounted on a single arbor, generally for simultaneous cutting.
- milling
milling
Machining operation in which metal or other material is removed by applying power to a rotating cutter. In vertical milling, the cutting tool is mounted vertically on the spindle. In horizontal milling, the cutting tool is mounted horizontally, either directly on the spindle or on an arbor. Horizontal milling is further broken down into conventional milling, where the cutter rotates opposite the direction of feed, or “up” into the workpiece; and climb milling, where the cutter rotates in the direction of feed, or “down” into the workpiece. Milling operations include plane or surface milling, endmilling, facemilling, angle milling, form milling and profiling.
- milling cutter
milling cutter
Loosely, any milling tool. Horizontal cutters take the form of plain milling cutters, plain spiral-tooth cutters, helical cutters, side-milling cutters, staggered-tooth side-milling cutters, facemilling cutters, angular cutters, double-angle cutters, convex and concave form-milling cutters, straddle-sprocket cutters, spur-gear cutters, corner-rounding cutters and slitting saws. Vertical cutters use shank-mounted cutting tools, including endmills, T-slot cutters, Woodruff keyseat cutters and dovetail cutters; these may also be used on horizontal mills. See milling.