Contact Details
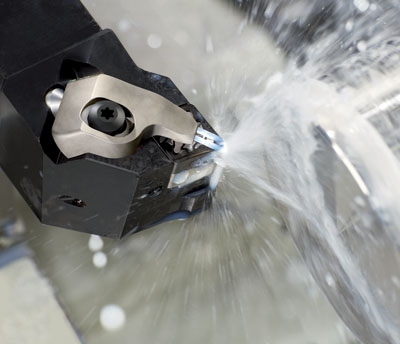
Walter has introduced Walter Turn Precision Coolant, a powerful and targeted coolant delivery system that produces a direct coolant supply through the insert clamp and along the flank face of the insert. The result is said to be a 30- to 150-percent increase in tool life (depending on material and coolant pressure) for stainless materials, high temperature alloys and steels.
The new system directs coolant precisely at the cutting edge providing greater lubrication, cooler inserts, and improved chip control, beginning at pressures as low as 150 psi. The positive effects increase with pressure, particularly at pressures above 580 psi. This can result in cutting speed improvements of up to 100% while maintaining the same tool life. Along with greater productivity, this improves surface finish with less peripheral zone work hardening, and boosts process reliability. Energy efficiency also benefits from the precisely targeted Walter Turn Precision Coolant system.
The new system is aimed primarily at ISO material groups P, M and S, with a pressure range of 150 to 2,250 psi. This range makes the system suitable for 95% of all machines in use today.
The new coolant delivery system features three coolant connection points: coolant hose connections at the back of the tool and under the head, and a direct coolant transfer port for VDI connections. Higher pressures up to approximately 4,500 psi are also possible, especially for aerospace applications.
Related Glossary Terms
- alloys
alloys
Substances having metallic properties and being composed of two or more chemical elements of which at least one is a metal.
- coolant
coolant
Fluid that reduces temperature buildup at the tool/workpiece interface during machining. Normally takes the form of a liquid such as soluble or chemical mixtures (semisynthetic, synthetic) but can be pressurized air or other gas. Because of water’s ability to absorb great quantities of heat, it is widely used as a coolant and vehicle for various cutting compounds, with the water-to-compound ratio varying with the machining task. See cutting fluid; semisynthetic cutting fluid; soluble-oil cutting fluid; synthetic cutting fluid.
- cutting speed
cutting speed
Tangential velocity on the surface of the tool or workpiece at the cutting interface. The formula for cutting speed (sfm) is tool diameter 5 0.26 5 spindle speed (rpm). The formula for feed per tooth (fpt) is table feed (ipm)/number of flutes/spindle speed (rpm). The formula for spindle speed (rpm) is cutting speed (sfm) 5 3.82/tool diameter. The formula for table feed (ipm) is feed per tooth (ftp) 5 number of tool flutes 5 spindle speed (rpm).
- hardening
hardening
Process of increasing the surface hardness of a part. It is accomplished by heating a piece of steel to a temperature within or above its critical range and then cooling (or quenching) it rapidly. In any heat-treatment operation, the rate of heating is important. Heat flows from the exterior to the interior of steel at a definite rate. If the steel is heated too quickly, the outside becomes hotter than the inside and the desired uniform structure cannot be obtained. If a piece is irregular in shape, a slow heating rate is essential to prevent warping and cracking. The heavier the section, the longer the heating time must be to achieve uniform results. Even after the correct temperature has been reached, the piece should be held at the temperature for a sufficient period of time to permit its thickest section to attain a uniform temperature. See workhardening.
Additional Products from Walter USA LLC
Pagination
- First page
- Previous page
- …
- 17
- 18
- 19
- 20
- 21
- 22
- 23
- 24
- 25