Contact Details
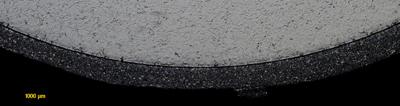
UltraFlex, a new portfolio of wear-resistant surface treatments from Kennametal, brings industry-leading wear performance to components with complex geometries in power generation, oil and gas, and many other industries. Combining Kennametal's expertise with tungsten carbide-based materials with super alloy-based technologies from Kennametal Stellite, UltraFlex provides metallurgical-bonded, void-free cladding that provides longer and more predictable service life for critical components in the most demanding environments.
Kennametal's UltraFlex portfolio provides a wide range of material solutions to protect against abrasive, erosive, corrosive, and galling wear needs for base materials including carbon and alloy steels, stainless steels, and cobalt and nickel alloys. With the ability to customize thickness and treat complex geometries, proprietary UltraFlex technology results in dramatically extended component life, more predictable wear and maintenance, higher productivity, and reduced operating costs.
Parts with complex geometries, inner diameters, and other non-line-of-sight features may encounter consistency problems with traditional thermal spray or weld overlay. By comparison, UltraFlex easily conforms to intricate shapes, small internal diameters, and reaches the remote locations that other hardfacing technologies cannot.
The UltraFlex surface treatment can be applied in a range of thicknesses, from approximately 0.254mm to 2.03mm (0.010" to 0.080"). Depending on the application, the smooth UltraFlex surface can be used "as applied" or machined to the desired finish.
Surface treatments with mechanical bonding may not stand up to harsh environments due to porosity and cracking. The proprietary UltraFlex process metallurgically bonds the wear system directly to the substrate, providing a surface with consistent thickness and minimal dilution. Solutions for Corrosion, Abrasion, and Erosion
Kennametal's expertise in metallurgical and materials science allows us to formulate, design, and deliver superior protection across the entire spectrum of corrosive and abrasive wear. UltraFlex product formulations draw from this depth and breadth of materials science, from cobalt-based alloys addressing corrosion resistance, to carbide composites for slowing abrasive and/or erosive wear.
For components such as severe service valves, the Stellite alloy-based grade of UltraFlex ensures that there is no cracking or de-lamination of the surface to protect the substrate.
For components such as the bottoms pumps in Fluid Catalytic Cracking units, harsh abrasion and erosion can destroy components within a matter of months. Kennametal's tungsten-carbide based solution, applied to the wetted surface of the component, has been proven to improve life by to up to four times.
A U.S. Gulf Coast refinery had recently experienced accelerated internal wear of oil pumps, often requiring entire case replacements. Compared to typical industry pump performance, run lengths were about a month shorter and maintenance-related costs were higher. The application requires pumps capable of withstanding significant catalyst fines. The refinery investigated several wear-resistant products for their pumps and found all were limited due to the nature of the technologies. Thermal spray coatings and weld overlays could be used in line-of-sight applications, but not for small interior surfaces.
The refinery found that thermal sprays also suffer from failures of the mechanical bond and there was preferential erosion of the soft matrix between the hard particles in weld overlays. Hard diffusion coatings (boronizing) are very thin and can be punctured by large abrasive particles.
Working with Kennametal, the refinery used infiltration brazed tungsten carbide cladding and UltraFlex to coat the inside of closed impellers unreachable by any other means. The company was particularly impressed by the true metallurgical bond and a dense, uniform distribution of tungsten carbide particles throughout the coating, which created excellent erosion resistance and toughness in complex geometries.
After 13 months in service, a treated oil pump showed no significant signs of internal erosion. This technology has also been applied to fluidized catalytic cracking unit (FCCU) fractionator bottoms and debutanizer reboiler services, with no signs to date of increased vibration or loss of hydraulic performance.
Modern valves control flow of all types, including: thin gasses, highly corrosive chemicals, superheated steam, abrasive slurries, toxic gases and radioactive materials. Valves can handle temperatures from subfreezing to molten metal, and pressures from high vacuum to thousands of pounds per square centimeter.
The severe service metal-seated ball valves used in harsh services are made of exotic metal alloys, and require coatings to protect the surfaces against a combination of corrosion and wear.
Thermal spray and Stellite weld overlay coatings are widely used to protect balls and seats. But as customers require improved performance for longer component life, new material solutions are needed. Kennametal has developed surface treatment technologies that metallurgically fuse advanced metal compositions onto balls and seats, resulting in exceptional wear and corrosion resistance in environments where chemicals are transported, often in combination of very high temperatures, or containing erosive particulates. UltraFlex technology enables Kennametal to select the most suitable coating material that will resist specific conditions, and offer customers engineered materials beyond standard coatings.
Velan, a leading valve manufacturer, has recently embraced UltraFlex technology, applying it on the severe service metal-seated ball valves, solving customer problems in the petrochemical industry.
Related Glossary Terms
- abrasive
abrasive
Substance used for grinding, honing, lapping, superfinishing and polishing. Examples include garnet, emery, corundum, silicon carbide, cubic boron nitride and diamond in various grit sizes.
- alloy steels
alloy steels
Steel containing specified quantities of alloying elements (other than carbon and the commonly accepted amounts of manganese, sulfur and phosphorus) added to cause changes in the metal’s mechanical and/or physical properties. Principal alloying elements are nickel, chromium, molybdenum and silicon. Some grades of alloy steels contain one or more of these elements: vanadium, boron, lead and copper.
- alloys
alloys
Substances having metallic properties and being composed of two or more chemical elements of which at least one is a metal.
- composites
composites
Materials composed of different elements, with one element normally embedded in another, held together by a compatible binder.
- corrosion resistance
corrosion resistance
Ability of an alloy or material to withstand rust and corrosion. These are properties fostered by nickel and chromium in alloys such as stainless steel.
- diffusion
diffusion
1. Spreading of a constituent in a gas, liquid or solid, tending to make the composition of all parts uniform. 2. Spontaneous movement of atoms or molecules to new sites within a material.
- galling
galling
Condition whereby excessive friction between high spots results in localized welding with subsequent spalling and further roughening of the rubbing surface(s) of one or both of two mating parts.
- stainless steels
stainless steels
Stainless steels possess high strength, heat resistance, excellent workability and erosion resistance. Four general classes have been developed to cover a range of mechanical and physical properties for particular applications. The four classes are: the austenitic types of the chromium-nickel-manganese 200 series and the chromium-nickel 300 series; the martensitic types of the chromium, hardenable 400 series; the chromium, nonhardenable 400-series ferritic types; and the precipitation-hardening type of chromium-nickel alloys with additional elements that are hardenable by solution treating and aging.
- tungsten carbide ( WC)
tungsten carbide ( WC)
Intermetallic compound consisting of equal parts, by atomic weight, of tungsten and carbon. Sometimes tungsten carbide is used in reference to the cemented tungsten carbide material with cobalt added and/or with titanium carbide or tantalum carbide added. Thus, the tungsten carbide may be used to refer to pure tungsten carbide as well as co-bonded tungsten carbide, which may or may not contain added titanium carbide and/or tantalum carbide.