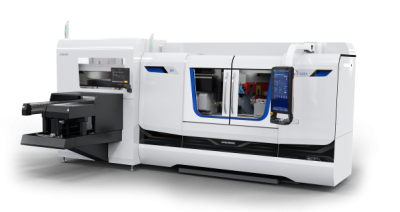
STUDER focuses on universality and speed with the uniLoad loading system. The automatic loading system enables users of the S31 and S33 external cylindrical grinding machines to increase quality and productivity.
Thanks to the modern and intuitive control, the system is so easy to operate that no special programming training is required. The control was developed by Wenger Automation and continues the STUDER operating philosophy. No programming skills are required. The user only needs to know the dimension and weight of the workpiece in order to use the loading system. The set-up wizard then guides the user conveniently through the necessary steps to start the grinding program.
uniLoad is offered on the basis of a linear portal cell with two parallel grippers and is suitable for shaft components up to a length of 350 mm and a diameter of max. 100 mm. It thus covers a large proportion of the component ranges produced on these machines. The parts are supplied via a standardized, adjustable V-belt. The housing for the base module, which is provided with a loading hatch as standard, has been adapted to suit the machine design and enables safe and clean operation of the system.
uniLoad is currently suitable for distances between centers of 650 and 1000mm. The loading system is docked onto the machine and with the racks at full capacity enables automated processing of around one hour. In the case of workpieces with an external diameter of 34mm and a gripper diameter of 22mm, 50 parts can be loaded automatically. The look of the loading system is reflected in the aesthetic design of the machine, and as a standard product enables quick response and delivery times. Customized solutions are also possible. In addition uniLoad is expandable, so that future requirements can also be met.
uniLoad in detail
- Siemens Simotion control
- Spectrum of parts: Shaft components
- Gripper with quick change jaws, convertible to:
- Gripper diameter min. Ø6 / max. Ø80
- Part weight max. 5 kg in alternating operation
- Part weight max. 15 kg in individual operation
- Maximum part size:
- Diameter 100 mm
- Length 10 - 350 mm
- Adjustable V-belt, finished parts conveyor and NOK box
- Intuitive 15’’ touch operating panel
Contact Details
Related Glossary Terms
- centers
centers
Cone-shaped pins that support a workpiece by one or two ends during machining. The centers fit into holes drilled in the workpiece ends. Centers that turn with the workpiece are called “live” centers; those that do not are called “dead” centers.
- cylindrical grinding
cylindrical grinding
Grinding operation in which the workpiece is rotated around a fixed axis while the grinding wheel is fed into the outside surface in controlled relation to the axis of rotation. The workpiece is usually cylindrical, but it may be tapered or curvilinear in profile. See centerless grinding; grinding.
- grinding
grinding
Machining operation in which material is removed from the workpiece by a powered abrasive wheel, stone, belt, paste, sheet, compound, slurry, etc. Takes various forms: surface grinding (creates flat and/or squared surfaces); cylindrical grinding (for external cylindrical and tapered shapes, fillets, undercuts, etc.); centerless grinding; chamfering; thread and form grinding; tool and cutter grinding; offhand grinding; lapping and polishing (grinding with extremely fine grits to create ultrasmooth surfaces); honing; and disc grinding.
- parallel
parallel
Strip or block of precision-ground stock used to elevate a workpiece, while keeping it parallel to the worktable, to prevent cutter/table contact.