Contact Details
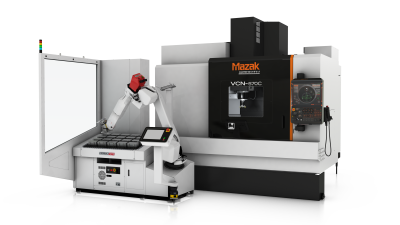
Mazak Corp.'s Kentucky-built VCN-570C vertical machining center paired with an integrated automation package and equipped with the company’s Smooth Synchronous Tapping Software. Designed to process large parts or multiple small workpieces in single machine setups, the VCN-570C brings advanced technology, performance and value to an expansive range of metalworking applications.
The VCN-570C can be optionally equipped with a robot interface, servo-driven automatic door and pneumatic fixture preparation to automatically clamp Schunk vises mounted in the machine. The machine also can incorporate a RoboJob TA200 automation package that includes a FANUC M20 articulating robot with a 44.1-lb. (20 kg) payload capacity, touch screen operator control and dedicated loading/unloading station.
The robot’s dual two-jaw grippers accommodate parts ranging from 0.39" to 5.90" (10 mm to 150 mm) in diameter, while the system’s fixed table can be configured with either workpiece supports or grid plates, depending on the application. The table and robot are unguarded and continuously monitored by an area scanner, which allows for easy operator access to load/unload parts from the table.
To ensure fast, accurate hole threading, the VCN-570C demonstrated Mazak’s Smooth Synchronous Tapping Software as part of its SmoothG control. With the software, the machine generates faster acceleration/deceleration with maximum spindle torque utilization. It does not overshoot at the bottom of a hole, and a faster time constant is
used that reduces overall tapping cycle times.
Mazak’s Mazatrol SmoothG CNC offers the flexibility of both EIA/ISO programming and Mazatrol conversational programming that makes it fast and easy to generate programs for quick changeover or handle high-production part applications. The control features advanced hardware and software functions such as Intelligent Pocket Milling software, which enables fast metal-removal rates in recessed pockets along with High-Gain Feed Forward Control, Variable Acceleration Control and Smooth Machining Configuration (SMC) for high-speed machining applications.
The VCN-570C’s 22.440" (570-mm) Y-axis stroke and 51.2" (1300 mm) operator door opening further increases part size, ease of part loading and processing versatility. Additionally, the machine comes equipped with a standard crane access door to allow loading of heavy parts more efficiently. Also contributing to the 3-axis machine’s productivity are a fast traverse rate of 1,654 ipm in the X, Y and Z axes.
Related Glossary Terms
- computer numerical control ( CNC)
computer numerical control ( CNC)
Microprocessor-based controller dedicated to a machine tool that permits the creation or modification of parts. Programmed numerical control activates the machine’s servos and spindle drives and controls the various machining operations. See DNC, direct numerical control; NC, numerical control.
- conversational programming
conversational programming
Method for using plain English to produce G-code file without knowing G-code in order to program CNC machines.
- feed
feed
Rate of change of position of the tool as a whole, relative to the workpiece while cutting.
- fixture
fixture
Device, often made in-house, that holds a specific workpiece. See jig; modular fixturing.
- gang cutting ( milling)
gang cutting ( milling)
Machining with several cutters mounted on a single arbor, generally for simultaneous cutting.
- inches per minute ( ipm)
inches per minute ( ipm)
Value that refers to how far the workpiece or cutter advances linearly in 1 minute, defined as: ipm = ipt 5 number of effective teeth 5 rpm. Also known as the table feed or machine feed.
- machining center
machining center
CNC machine tool capable of drilling, reaming, tapping, milling and boring. Normally comes with an automatic toolchanger. See automatic toolchanger.
- metalworking
metalworking
Any manufacturing process in which metal is processed or machined such that the workpiece is given a new shape. Broadly defined, the term includes processes such as design and layout, heat-treating, material handling and inspection.
- milling
milling
Machining operation in which metal or other material is removed by applying power to a rotating cutter. In vertical milling, the cutting tool is mounted vertically on the spindle. In horizontal milling, the cutting tool is mounted horizontally, either directly on the spindle or on an arbor. Horizontal milling is further broken down into conventional milling, where the cutter rotates opposite the direction of feed, or “up” into the workpiece; and climb milling, where the cutter rotates in the direction of feed, or “down” into the workpiece. Milling operations include plane or surface milling, endmilling, facemilling, angle milling, form milling and profiling.
- overshoot
overshoot
Deviation from nominal path caused by momentum carried over from previous step, as when a tool is rapidly traversed a considerable distance to begin a cut. Usually applies to CNC machining and is prevented if the control has the appropriate look-ahead capability. See look-ahead; undershoot.
- payload ( workload)
payload ( workload)
Maximum load that the robot can handle safely.
- tapping
tapping
Machining operation in which a tap, with teeth on its periphery, cuts internal threads in a predrilled hole having a smaller diameter than the tap diameter. Threads are formed by a combined rotary and axial-relative motion between tap and workpiece. See tap.
- threading
threading
Process of both external (e.g., thread milling) and internal (e.g., tapping, thread milling) cutting, turning and rolling of threads into particular material. Standardized specifications are available to determine the desired results of the threading process. Numerous thread-series designations are written for specific applications. Threading often is performed on a lathe. Specifications such as thread height are critical in determining the strength of the threads. The material used is taken into consideration in determining the expected results of any particular application for that threaded piece. In external threading, a calculated depth is required as well as a particular angle to the cut. To perform internal threading, the exact diameter to bore the hole is critical before threading. The threads are distinguished from one another by the amount of tolerance and/or allowance that is specified. See turning.