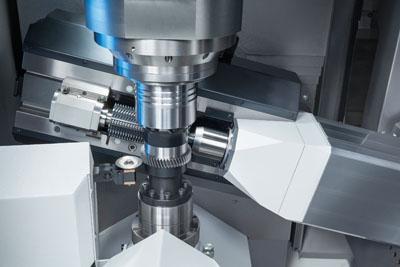
Gear cutting requirements, for example in the manufacture of powertrain components, continue the trend of becoming increasingly stringent. Complex gearbox configurations pose enormous component quality challenges, especially when produced in ever larger quantities. With the new VLC series of modular machines, including the VLC 200 H vertical gear hobbing machine and the VLC 100 C vertical chamfering machine, EMAG offers a solution to meet these production challenges.
When it comes to the gear cutting process, the experts at EMAG subsidiary KOEPFER in Germany are reportedly the ideal contact within the EMAG Group. A highly innovative company that has been extremely successful in the gear sector, the company keeps a close eye on the developments and consistently changing demands in the industry. In response, the VLC 200 H vertical gear hobbing machine is the first in EMAG's new modular design concept with integrated KOEPFER technology.
The modular platform from EMAG combines the various EMAG Group technologies on the same basic machine design, with the pick-up principle being employed on all of them. Each modular machine also features a component storage element, from which the pick-up spindle collects the raw parts and to which it returns them again finish-machined, resulting in minimized chip-to-chip times. The vertical construction of the machine guarantees ideal chip flow conditions, preventing any build-up and providing for a consistently high manufacturing quality. The machine design also allows for the compact arrangement of the spindle, slides and automation belt, reducing the floorspace requirement. The uniform construction of these modular machines makes them ideal for incorporation into production lines, as the component transfer height between machines is always the same.
The VLC 200 H vertical gear hobbing machine features technology that also offers many economic advantages when used in its stand-alone version. The high-performance drives on the main spindle and hob offer torque rates and speeds to guarantee highly productive gear cutting with a max diameter of 200mm and module 4, allowing them to be dry-milled in short cycle times. To achieve a consistently optimal component quality, the VLC 200 H can be equipped with an optional slide-mounted measuring system. As this is located outside the machining area, it is protected from chips and dirt and can be swung out of the way, if required. It is also possible to equip the measuring station with a probe for the quality control of components and a sensor system for component orientation. This allows machining operations to be adjusted at any time while simultaneously keeping a running record for quality control purposes.
As is the case after every gear cutting operation, hobbing on the VLC 200 H poses the question of how the tooth profile can be chamfered with the highest contour accuracy. The VLC 100 C chamfering machine can be equipped with the relevant technology to suit every requirement.
"Which of the technologies we use depends mainly on the workpiece to be machined. We have a choice of bevel chamfering and the newer CHAMFER-CUT," explains Jörg Lohmann, Head of Sales at EMAG KOEPFER.
The classic bevel chamfering process, well established in the automotive industry and amongst its sub-suppliers, is used whenever the workpiece geometry features contour traps requiring it. This is primarily the case with shaft workpieces that feature a hub or with gears featuring a synchronizer ring. It must be emphasized that the tool used in these cases can be easily and cost-efficiently re-sharpened by the user, in contrast to products from other manufacturers, reducing both tooling and storage costs for new pieces. For workpieces with a more favorable geometry, the VLC 100 C is equipped for use of the CHAMFER-CUT method. This method, developed by FETTE, is ideal at aiming for a cost-efficient, precision chamfering process.
"As this method does not throw up a secondary burr, it is particularly suitable for gearings that are being honed after hardening," explains Lohmann. The CHAMFER-CUT process is carried out in two steps, with the upper surface of the gear contour being chamfered with high accuracy first. The cutting direction is then reversed and the process repeated on the underside of the gear. "Regardless of the machine demands made by the workpiece and its geometry, EMAG KOEPFER always offers an excellent solution,"
Contact Details
Related Glossary Terms
- burr
burr
Stringy portions of material formed on workpiece edges during machining. Often sharp. Can be removed with hand files, abrasive wheels or belts, wire wheels, abrasive-fiber brushes, waterjet equipment or other methods.
- chamfering
chamfering
Machining a bevel on a workpiece or tool; improves a tool’s entrance into the cut.
- hardening
hardening
Process of increasing the surface hardness of a part. It is accomplished by heating a piece of steel to a temperature within or above its critical range and then cooling (or quenching) it rapidly. In any heat-treatment operation, the rate of heating is important. Heat flows from the exterior to the interior of steel at a definite rate. If the steel is heated too quickly, the outside becomes hotter than the inside and the desired uniform structure cannot be obtained. If a piece is irregular in shape, a slow heating rate is essential to prevent warping and cracking. The heavier the section, the longer the heating time must be to achieve uniform results. Even after the correct temperature has been reached, the piece should be held at the temperature for a sufficient period of time to permit its thickest section to attain a uniform temperature. See workhardening.
- modular design ( modular construction)
modular design ( modular construction)
Manufacturing of a product in subassemblies that permits fast and simple replacement of defective assemblies and tailoring of the product for different purposes. See interchangeable parts.
- quality assurance ( quality control)
quality assurance ( quality control)
Terms denoting a formal program for monitoring product quality. The denotations are the same, but QC typically connotes a more traditional postmachining inspection system, while QA implies a more comprehensive approach, with emphasis on “total quality,” broad quality principles, statistical process control and other statistical methods.