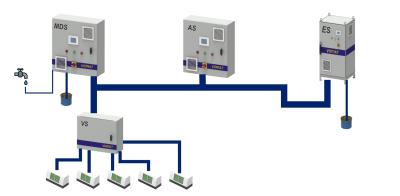
Water-miscible cooling lubricants represent a cost-optimized alternative to their non-water-soluble counterparts in many grinding operations in the metalworking industry. To ensure that the emulsions and solutions can remain in the system for a long time, precise metering and mixing is crucial. In addition, it must be ensured that process-destabilizing contaminants are identified and removed at an early stage during use. Until now, this was often a manual inspection and additional task that the machine operator constantly performed during the grinding process. A new system for dosing, mixing and maintaining water-miscible cooling lubricants from the filter specialist Vomat in Treuen provides a remedy. The Vomat system is made up of various modules, ensures the correct dosing and mixing of water and concentrate fully automatically before and during use, detects contaminants during the process and extracts them. A special distribution unit also allows the connection of several grinding machines.
Thanks to their high water content, water-miscible cooling lubricants have, among other things, a very good cooling effect. The additives optimize the physical, chemical and tribological properties of the cooling lubricant. Optimally dosed and mixed, modern emulsions and solutions thus make a significant contribution to process stability, reduced maintenance requirements and minimized coolant and ancillary costs in their simple as well as economical use in certain grinding applications. In addition, they increase workplace safety and sustainably conserve resources and the environment.
However, the application properties of water-miscible cooling lubricants can be quickly changed by various interfering factors: One disadvantage compared with non-water-miscible cooling lubricants is their poor resistance to microorganisms. Infestation by fungi, bacteria, yeasts, etc. reduces the durability and corrosion protection of the emulsions. The hygienic conditions for the operating personnel deteriorate. Cooling lubricants contaminated with germs can, for example, cause serious health problems after contact with the skin. But a cooling lubricant with a high microbial load also poses a problem for the workpiece, tool and machine, since discoloration of the machined parts, shorter tool life and corrosion can be the result. In addition, water-miscible coolants lose stability due to infestation by microorganisms. This not only reduces tool life, but can also cause operational problems and machine downtime.
Stefen Strobel, Sales Manager at Vomat, says, "The service life of a cooling lubricant depends not only on product quality and the machining process, but also to a large extent on monitoring and the maintenance technology used, its scope and continuity. In order to use the water-mixed coolants economically and to achieve the desired grinding qualities as well as cost reductions, it is therefore imperative to maintain the service properties of the products used for as long as possible. Regular monitoring of the cooling lubricants with corrective measures is therefore necessary for use with long service lives and for the lowest possible risk potential for people and the environment. In this way, it is possible to react quickly and effectively, for example, in the event of mixture fluctuations and impurities, etc. This is not only important from the point of view of the lubricants themselves. This is not only important from the point of view of service life optimization. The user is also required by law to keep the cooling lubricant in perfect condition for the purposes of occupational safety and also to record its monitoring."
Increase process reliability and save time and costs
With a fully automatic maintenance system, Vomat now makes the use of water-miscible MWF even more time- and cost-optimized. The system has a modular design and can be integrated into the respective conditions of each grinding system as required.
The heart of the system is the fully automatic mixing and dosing system (MDS) with a tank size of up to 10,000 liters, which constantly regulates the defined ratio of water quantity and coolant concentrate with high precision. Steffen Strobel: "During grinding, there are drag-out losses, and some of the cooling lubricant also evaporates, so that the quantity and mixing ratio of water and concentrate are constantly changing. This can negatively affect the usage properties and shorten the service life. It is therefore important that the machine operator continuously checks the mixing ratio and can take corrective action if necessary. Our MDS now takes over this manual process, including the prescribed logging. This saves time, costs and significantly increases process reliability."
In addition, the grinder can use an analysis module (AS) that identifies process-destabilizing contaminants, such as particles from the grinding process, and determines their content. A special extrusion system (ES) removes these contaminants.
Steffen Strobel: "Our new maintenance system is modular, energy-efficient and compact. It helps to significantly increase the service life of water-miscible cooling lubricants in grinding processes. And a special distribution unit even allows the connection of several grinding machines."
Contact Details
Related Glossary Terms
- coolant
coolant
Fluid that reduces temperature buildup at the tool/workpiece interface during machining. Normally takes the form of a liquid such as soluble or chemical mixtures (semisynthetic, synthetic) but can be pressurized air or other gas. Because of water’s ability to absorb great quantities of heat, it is widely used as a coolant and vehicle for various cutting compounds, with the water-to-compound ratio varying with the machining task. See cutting fluid; semisynthetic cutting fluid; soluble-oil cutting fluid; synthetic cutting fluid.
- extrusion
extrusion
Conversion of an ingot or billet into lengths of uniform cross section by forcing metal to flow plastically through a die orifice.
- grinding
grinding
Machining operation in which material is removed from the workpiece by a powered abrasive wheel, stone, belt, paste, sheet, compound, slurry, etc. Takes various forms: surface grinding (creates flat and/or squared surfaces); cylindrical grinding (for external cylindrical and tapered shapes, fillets, undercuts, etc.); centerless grinding; chamfering; thread and form grinding; tool and cutter grinding; offhand grinding; lapping and polishing (grinding with extremely fine grits to create ultrasmooth surfaces); honing; and disc grinding.
- metalworking
metalworking
Any manufacturing process in which metal is processed or machined such that the workpiece is given a new shape. Broadly defined, the term includes processes such as design and layout, heat-treating, material handling and inspection.
- modular design ( modular construction)
modular design ( modular construction)
Manufacturing of a product in subassemblies that permits fast and simple replacement of defective assemblies and tailoring of the product for different purposes. See interchangeable parts.