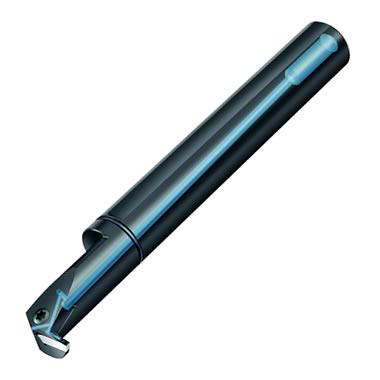
Walter has unveiled the Walter Cut G1221-P, an innovative grooving boring bar with precision cooling, for recessing and internal grooving. This monoblock boring bar has two coolant holes.
The first coolant hole allows the coolant to exit the insert top clamp directly to the cutting edge in the radial groove, thus providing precision cooling. The other coolant hole, at the front of the bar, can either be left open to evacuate chips out of a blind bore, or sealed off when in a through-bore to provide increased coolant to the cutting edge.
Additionally, an O-ring is recessed into the bar clamping diameter to prevent pressure loss and provide leak free coolant supply to the cutting interface. This is particularly helpful on machines with low coolant pressure. Together with Walter's new UF8 chip geometry, the combination yields superior process reliability and productivity, excellent surface quality, and longer tool life.
Another advantage of the new Walter Cut G1221-P is that it can be used in both the normal and overhead position. This boring bar system holds GX09 and GX16 inserts. The insert widths go from 0.062 to 0.125 in. (0.8 to 3.5 mm). The system is suitable for internal grooves from Dmin = 0.63 in. (16 mm) and for grooving up to depths of 0.39 in. (10 mm) in all ISO material groups.
Contact Details
Related Glossary Terms
- boring
boring
Enlarging a hole that already has been drilled or cored. Generally, it is an operation of truing the previously drilled hole with a single-point, lathe-type tool. Boring is essentially internal turning, in that usually a single-point cutting tool forms the internal shape. Some tools are available with two cutting edges to balance cutting forces.
- boring bar
boring bar
Essentially a cantilever beam that holds one or more cutting tools in position during a boring operation. Can be held stationary and moved axially while the workpiece revolves around it, or revolved and moved axially while the workpiece is held stationary, or a combination of these actions. Installed on milling, drilling and boring machines, as well as lathes and machining centers.
- coolant
coolant
Fluid that reduces temperature buildup at the tool/workpiece interface during machining. Normally takes the form of a liquid such as soluble or chemical mixtures (semisynthetic, synthetic) but can be pressurized air or other gas. Because of water’s ability to absorb great quantities of heat, it is widely used as a coolant and vehicle for various cutting compounds, with the water-to-compound ratio varying with the machining task. See cutting fluid; semisynthetic cutting fluid; soluble-oil cutting fluid; synthetic cutting fluid.
- grooving
grooving
Machining grooves and shallow channels. Example: grooving ball-bearing raceways. Typically performed by tools that are capable of light cuts at high feed rates. Imparts high-quality finish.
- recessing
recessing
A turning operation in which a groove is produced on the periphery or inside a hole of a workpiece. The grooving tool moves at right angles to the axis of rotation.