Contact Details
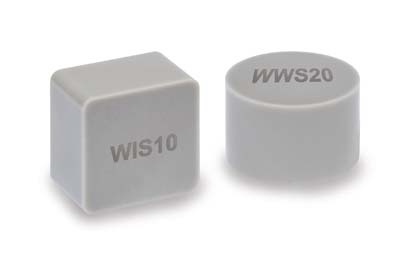
Walter USA LLC has introduced a new series of ceramic inserts directed at machining high-temp alloys such as Inconel, Waspalloy and Stellite. The new inserts feature grades WIS10 and WWS20.
Superalloys, because of the high cutting temperatures generated with greater tool stresses and increased tool wear, can be very tough on carbide tools typically used to machine them. Ceramics, though, because of their extreme hardness, heat resistance and wear resistance, can stand up to these demanding applications.
Walter's two new complimentary grades, silicon nitride-based WIS10 (Sialon ceramic) and WWS20 with Whisker silicon carbides (Whisker ceramic), do more than simply stand up to these applications with increased tool life and process reliability, they also deliver cutting speeds five to ten times higher than carbide in roughing and semi-finishing operations.
With its self-reinforced structure of silicon nitride ceramics and enhanced chemical stability, WIS10 offers excellent notch wear resistance and excels at machining all types of heat resistant high temp alloys. WWS20 offers superior fracture and crack resistance thanks to its "Whisker fibers," and is ideal for nickel-based alloys and difficult conditions, such as machining forged out-of-round workpieces with uneven surfaces. It also excels at hard machining of steel.
Walter supplies ceramic inserts in diamond, round and square shapes (CN, DN, RC, RP, RN and SN formats), with different cutting edge designs for turning and milling. In addition, Walter supplies toolholders with carbide shoe and clamping system. This gives the user the best possible toolholder systems for turning with the new ceramic indexable inserts.
The demand for high temperature superalloy parts is constantly increasing, with particularly significant growth recently in the aerospace, energy, petrochemical and medical industries. These industries require components that are highly corrosion-resistant and/or resistant to high temperatures.
Related Glossary Terms
- alloys
alloys
Substances having metallic properties and being composed of two or more chemical elements of which at least one is a metal.
- ceramics
ceramics
Cutting tool materials based on aluminum oxide and silicon nitride. Ceramic tools can withstand higher cutting speeds than cemented carbide tools when machining hardened steels, cast irons and high-temperature alloys.
- gang cutting ( milling)
gang cutting ( milling)
Machining with several cutters mounted on a single arbor, generally for simultaneous cutting.
- hardness
hardness
Hardness is a measure of the resistance of a material to surface indentation or abrasion. There is no absolute scale for hardness. In order to express hardness quantitatively, each type of test has its own scale, which defines hardness. Indentation hardness obtained through static methods is measured by Brinell, Rockwell, Vickers and Knoop tests. Hardness without indentation is measured by a dynamic method, known as the Scleroscope test.
- milling
milling
Machining operation in which metal or other material is removed by applying power to a rotating cutter. In vertical milling, the cutting tool is mounted vertically on the spindle. In horizontal milling, the cutting tool is mounted horizontally, either directly on the spindle or on an arbor. Horizontal milling is further broken down into conventional milling, where the cutter rotates opposite the direction of feed, or “up” into the workpiece; and climb milling, where the cutter rotates in the direction of feed, or “down” into the workpiece. Milling operations include plane or surface milling, endmilling, facemilling, angle milling, form milling and profiling.
- superalloys
superalloys
Tough, difficult-to-machine alloys; includes Hastelloy, Inconel and Monel. Many are nickel-base metals.
- toolholder
toolholder
Secures a cutting tool during a machining operation. Basic types include block, cartridge, chuck, collet, fixed, modular, quick-change and rotating.
- turning
turning
Workpiece is held in a chuck, mounted on a face plate or secured between centers and rotated while a cutting tool, normally a single-point tool, is fed into it along its periphery or across its end or face. Takes the form of straight turning (cutting along the periphery of the workpiece); taper turning (creating a taper); step turning (turning different-size diameters on the same work); chamfering (beveling an edge or shoulder); facing (cutting on an end); turning threads (usually external but can be internal); roughing (high-volume metal removal); and finishing (final light cuts). Performed on lathes, turning centers, chucking machines, automatic screw machines and similar machines.
- wear resistance
wear resistance
Ability of the tool to withstand stresses that cause it to wear during cutting; an attribute linked to alloy composition, base material, thermal conditions, type of tooling and operation and other variables.