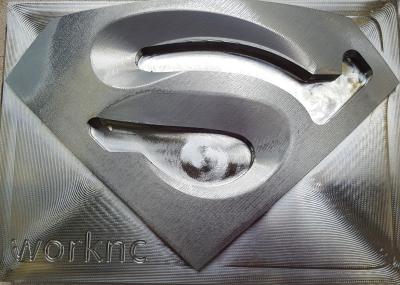
Vero Software has launched the latest version of WorkNC, a specialized CAD/CAM software package for 2- to 5- axis machining. WorkNC 2017 R2 takes advantage of the latest improvements made to the Vero Software Waveform Roughing strategy.
"Faster and safer than ever, the Waveform strategy significantly improves standard roughing technologies with its consistent material removal while increasing the tool and machine service life,” said WorkNC Brand Manager Miguel Johann.
WorkNC Waveform Roughing takes further strides in 2017 R2 by reducing machining times, as well as improving cutting conditions. Toolpath optimization is achieved by taking tool load into consideration during intermediate Z-step calculations.
"The Waveform technology has been designed to perform roughing operations at very high speeds and requires toolpath security control,” Johann said.
A new option allows users to force the initial lead-in and the final lead-out to a secure point above the stock in case of a difference between the virtual stock and the real stock on the machine. “WorkNC 2017R2 fulfills the users' quest for further time savings and optimal surface quality,” Johann said.
The new Parallel Finishing toolpath makes use of the Advanced Toolform technology, which offers efficient high-feed cutter management. Toolpath calculations are based on the real shape of the cutter, which ensures optimal surface quality and machining times reduced by up to 80 percent, according to the company.
The Die Flats Finishing toolpath now features a new option that enables radial stepovers to ensures a fluid trajectory and the elimination of sharp angles. This results in improved surface quality and reduced machining times.
Johann said WorkNC has long been recognized for its standard collision-detection functions, covering machining environment, toolholder, stock and the machining center to secure toolpaths. WorkNC 2017R2 further enhances process security by systematically calculating collisions and out-of-limit conditions.
The CAD module has also been improved in 2017 R2. All machining preparation operations (part, machining setup, clamping systems) can now be carried out in the CAD module. When creating a workzone, the complete assembly is exported into the machining context at the same time as the part itself. It's no longer required to reposition assemblies with respect to the part.
In 2017 R2, WorkNC automates and simplifies the machining sequence process, giving step-by-step assistance during toolpath programming. The machining sequence process now informs the user of any missing data in the workzone, such as views, curves and points, allowing for last-minute corrections.
"WorkNC is also investing for the future. The latest version introduces its educational license to prepare tomorrow's users. WorkNC for Education includes a student edition, giving students the opportunity to practice their skills and gain experience in all the latest CAM strategies,” Johann said.
Contact Details
Related Glossary Terms
- computer-aided design ( CAD)
computer-aided design ( CAD)
Product-design functions performed with the help of computers and special software.
- computer-aided manufacturing ( CAM)
computer-aided manufacturing ( CAM)
Use of computers to control machining and manufacturing processes.
- machining center
machining center
CNC machine tool capable of drilling, reaming, tapping, milling and boring. Normally comes with an automatic toolchanger. See automatic toolchanger.
- parallel
parallel
Strip or block of precision-ground stock used to elevate a workpiece, while keeping it parallel to the worktable, to prevent cutter/table contact.
- toolholder
toolholder
Secures a cutting tool during a machining operation. Basic types include block, cartridge, chuck, collet, fixed, modular, quick-change and rotating.
- toolpath( cutter path)
toolpath( cutter path)
2-D or 3-D path generated by program code or a CAM system and followed by tool when machining a part.