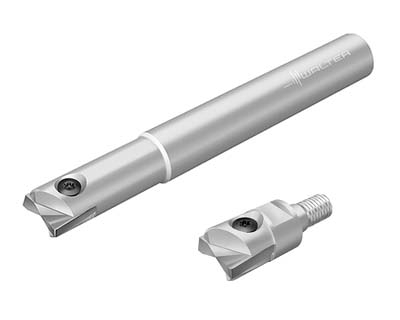
Walter USA LLC has introduced the new F4031 Xtra-tec Toric copy mill. The new cutter features a Torx Plus screw that permits improved handling along with higher clamping and unclamping torque. It also offers precise positioning of the insert via an innovative prism design, and insert clamping with fitting bolt to secure optimal clamping and centering. In addition, the tool boasts a PVD coated body for enhanced wear resistance and longer life.
The F4031 features a Toric, positive insert for superior accuracy. These inserts are completely ground, that is, circumference, prism and thickness, and hold a corner radius accuracy of +/- 0.0004-in., and a 90 degree secondary cutting edge.
Field tests of the new F4031 copy mill have yielded superior results in the mold and die industry as well as in semi-finishing and finishing operations. Excellent results have also been achieved particularly in terms of tool life and cutting costs, with steel, stainless steel, cast iron, difficult to cut materials and in hard machining. Diameters for the copy mill range from 12 to 32mm (0.312 to 1.250").
Additional benefits of the F4031 include: secondary operations are virtually eliminated because of the high surface quality on flat areas or on shoulders due to the precise ground geometry; high process reliability due to the aforementioned prism design and clamping of the insert; reduced storage costs stemming from the fact that this single tool can be adapted to a variety of applications; and no need for the regrinding costs and delays often associated with solid carbide tools.
Contact Details
Related Glossary Terms
- centering
centering
1. Process of locating the center of a workpiece to be mounted on centers. 2. Process of mounting the workpiece concentric to the machine spindle. See centers.
- flat ( screw flat)
flat ( screw flat)
Flat surface machined into the shank of a cutting tool for enhanced holding of the tool.
- milling machine ( mill)
milling machine ( mill)
Runs endmills and arbor-mounted milling cutters. Features include a head with a spindle that drives the cutters; a column, knee and table that provide motion in the three Cartesian axes; and a base that supports the components and houses the cutting-fluid pump and reservoir. The work is mounted on the table and fed into the rotating cutter or endmill to accomplish the milling steps; vertical milling machines also feed endmills into the work by means of a spindle-mounted quill. Models range from small manual machines to big bed-type and duplex mills. All take one of three basic forms: vertical, horizontal or convertible horizontal/vertical. Vertical machines may be knee-type (the table is mounted on a knee that can be elevated) or bed-type (the table is securely supported and only moves horizontally). In general, horizontal machines are bigger and more powerful, while vertical machines are lighter but more versatile and easier to set up and operate.
- physical vapor deposition ( PVD)
physical vapor deposition ( PVD)
Tool-coating process performed at low temperature (500° C), compared to chemical vapor deposition (1,000° C). Employs electric field to generate necessary heat for depositing coating on a tool’s surface. See CVD, chemical vapor deposition.
- wear resistance
wear resistance
Ability of the tool to withstand stresses that cause it to wear during cutting; an attribute linked to alloy composition, base material, thermal conditions, type of tooling and operation and other variables.