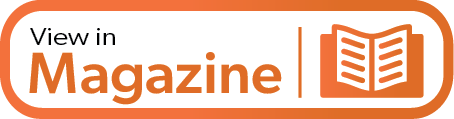
The ANCA Tool of the Year Awards 2024, which culminated with a special presentation at the ANCA booth during IMTS 2024, celebrated diversity within the industry and achievements in precision tool manufacturing.
“For 50 years,” said ANCA Co- Founder Pat Boland, “ANCA’s software has set industry standards, enabling Tool of the Year entrants to push the boundaries of what’s possible. Our technology not only meets the highest precision demands but also showcases the creativity and capability of our customers, highlighting truly innovative designs.”
Stephanie Chrystal from Sandvik Coromant USA was recognized as ANCA’s Female Machinist of the Year.
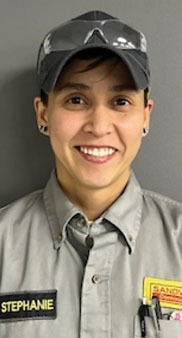
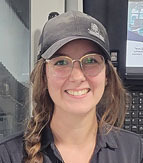
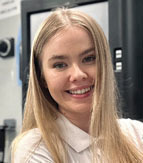
The award, introduced in 2023 to promote inclusivity, honors Chrystal’s problem-solving skills, leadership in expanding and training her team, and her ability to deliver outstanding results under pressure. Chrystal expressed pride in representing women in a typically male-dominated field, hoping to inspire others to pursue technical careers.
“It is a privilege to be a part of Sandvik Coromant, which is paving the way for women to be recognized for their contributions to the industry,” Chrystal said. “I am honored to have been chosen out of all of the extraordinary women in this field as the Female Machinist of the Year for ANCA. I hope to be an encouragement to women looking for guidance on their journey for meaningful careers. I am excited to see ANCA continue to honor women in this industry and inspire other companies with this award.”
ANCA also recognized Female Machinist of the Year finalists Roksana Grodowska of CNC Progresja Sp. z o.o., Poland, and Jessica Sennott of U.S.-based Gorilla Mill.
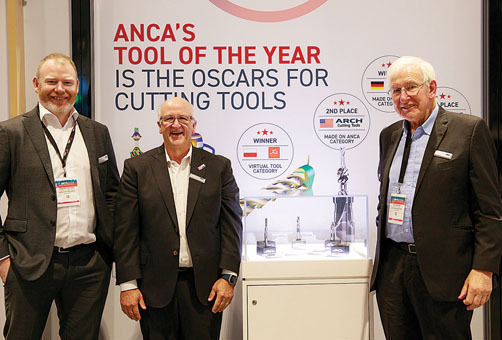
Werkzeugschleiferei Krämer GmbH won the Made on ANCA category, showcasing advanced use of ANCA’s iGrind operations and advanced profile software features, such as layers, pivot editor and 3D hook compensation.
“This tool is used by one of our customers to create a profile in a gripper for molded parts. Previously, this contour was produced using a 3D milling process,” said Torsten Mende, managing director at Werkzeugschleiferei Krämer GmbH. The customer’s tolerance specification was +/-0.01 mm. The program was created in ToolRoom RN32/33 and ground using RN34.1 on ANCA’s FX7.
“As a smaller company, it is a great honor to participate in this competition,” Mende added. “We have been grinding tools on ANCA machines since 1999. The sophisticated software enables us to grind complex geometries and to monitor them during the process, giving our customers a competitive advantage. For this reason, we extend our heartfelt thanks to ANCA for the excellent symbiosis of software and machines.”
ARCH Cutting Tools took second place in the category for its “Master Mill Combo Tool,” which continues to lead in multifunction cutting tools with exceptional accuracy utilizing iGrind software’s advanced profile operation features.
Precision Tool Co. earned third place for a versatile tool combining a drill, reamer and chamfer that was optimized using iGrind software for performance and functionality.
In the Virtual Tool Category, XGE impressed the judges with a creative and technically sophisticated entry inspired by the renowned attractions of the Garden Expo Park in Xiamen, China, including the Moonlight Ring and Xinglin Pavilion. Their design integrates iGrind software with pro-file and end-face operations, and is brought to life by importing 3D models into CIM3D software.
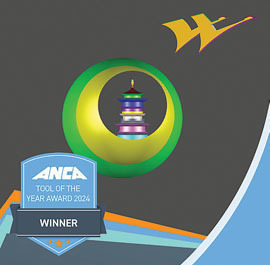
“This award is a high recognition of our team’s innovative capabilities,” said Chen Jianming, R&D engineer at XGE. “Our design was inspired by the ‘Moonlight Ring’ and ‘Xinglin Pavilion’ of Xiamen Yuanboyuan, symbolizing the harmony of nature and humanity. The egret in the design, replaced by our company logo, represents both a tribute to our brand and a leap in tool innovation.”
Second place in this category went to Zakłady Mechaniczne Kazimieruk for its simulation of the Olympic flame that was created with extensive iGrind software use.
Third place went to SST Cutting Tools for the company’s “LINGAM” simulation symbolizing the Hindu God Shiva. The simulation showcases creative use of iGrind software for profile, cross-section profile, and ripper form relief operations.
Related Glossary Terms
- computer numerical control ( CNC)
computer numerical control ( CNC)
Microprocessor-based controller dedicated to a machine tool that permits the creation or modification of parts. Programmed numerical control activates the machine’s servos and spindle drives and controls the various machining operations. See DNC, direct numerical control; NC, numerical control.
- gang cutting ( milling)
gang cutting ( milling)
Machining with several cutters mounted on a single arbor, generally for simultaneous cutting.
- grinding
grinding
Machining operation in which material is removed from the workpiece by a powered abrasive wheel, stone, belt, paste, sheet, compound, slurry, etc. Takes various forms: surface grinding (creates flat and/or squared surfaces); cylindrical grinding (for external cylindrical and tapered shapes, fillets, undercuts, etc.); centerless grinding; chamfering; thread and form grinding; tool and cutter grinding; offhand grinding; lapping and polishing (grinding with extremely fine grits to create ultrasmooth surfaces); honing; and disc grinding.
- milling
milling
Machining operation in which metal or other material is removed by applying power to a rotating cutter. In vertical milling, the cutting tool is mounted vertically on the spindle. In horizontal milling, the cutting tool is mounted horizontally, either directly on the spindle or on an arbor. Horizontal milling is further broken down into conventional milling, where the cutter rotates opposite the direction of feed, or “up” into the workpiece; and climb milling, where the cutter rotates in the direction of feed, or “down” into the workpiece. Milling operations include plane or surface milling, endmilling, facemilling, angle milling, form milling and profiling.
- milling machine ( mill)
milling machine ( mill)
Runs endmills and arbor-mounted milling cutters. Features include a head with a spindle that drives the cutters; a column, knee and table that provide motion in the three Cartesian axes; and a base that supports the components and houses the cutting-fluid pump and reservoir. The work is mounted on the table and fed into the rotating cutter or endmill to accomplish the milling steps; vertical milling machines also feed endmills into the work by means of a spindle-mounted quill. Models range from small manual machines to big bed-type and duplex mills. All take one of three basic forms: vertical, horizontal or convertible horizontal/vertical. Vertical machines may be knee-type (the table is mounted on a knee that can be elevated) or bed-type (the table is securely supported and only moves horizontally). In general, horizontal machines are bigger and more powerful, while vertical machines are lighter but more versatile and easier to set up and operate.
- reamer
reamer
Rotating cutting tool used to enlarge a drilled hole to size. Normally removes only a small amount of stock. The workpiece supports the multiple-edge cutting tool. Also for contouring an existing hole.
- relief
relief
Space provided behind the cutting edges to prevent rubbing. Sometimes called primary relief. Secondary relief provides additional space behind primary relief. Relief on end teeth is axial relief; relief on side teeth is peripheral relief.
- tolerance
tolerance
Minimum and maximum amount a workpiece dimension is allowed to vary from a set standard and still be acceptable.